A Closer Look at Hydraulic Oil Viscosity Classification Systems
1. Introduction
Viscosity is the most important criterion in choosing a hydraulic oil which comes from its direct impact on pump life as the beating heart of the hydraulic circuit, especially in mining machinery. The extreme working conditions within the mining industry place enormous demands on equipment with hydraulic systems. The result is often loss of power, productivity, and reduced fuel economy. Among the people of industry, there is a common misconception that reducing hydraulic fluid nominal viscosity will decrease hydraulic circuit operating temperatures. This misconception is based on the fact that higher viscosities may lead to a reduction in hydraulic applications which in turn take the operating fluid further away from thermal shock occurrence which means a longer life for hydraulic fluid and pumps [1]. On the contrary, in order to reduce the operating temperature of the system, the viscosity of the oil must be increased by one grade. This is because a hydraulic fluid that is too low in viscosity will reduce the pump’s volumetric efficiency and cause fluid overheating [1].
After all, the use of hydraulic oil with a viscosity lower than the required amount will lead to an increase in friction between the surfaces of the load carrier in the pump which leads to erosion increase. On the other hand, choosing a hydraulic oil with a viscosity greater than wanted will also cause problems in the pump, decreasing its mechanical efficiency, and erosion caused by cavitation [2,3]. Therefore, choosing the right viscosity for hydraulic oil will definitely lead to maintaining the volumetric and mechanical efficiency of the pump (see Figure 1).
![Figure 1: Effect of oil viscosity on the volumetric and mechanical efficiency of a hydraulic pump [2-5]](img/Ahmadreza-Aminian-ARTICLE-images-1.jpg)
As the importance of choosing the correct viscosity for a hydraulic oil is revealed, the lubrication expert needs to know the viscosity classification system for using hydraulic oils. This article intends to discuss all these systems in detail. Among the various classification systems used to express the viscosity grade for hydraulic oils, two most common systems will be discussed in this article: the ISO classification system, the GOST classification system, and the ASTM system of classification for hydraulic oils.
2. ISO system
In 1975, a joint cooperation between the standardization bodies of several countries, including ASTM (the USA), STLE (the USA), BSI (England), and DIN (Germany) was formed aiming to standardize a viscosity classification system for industrial oils.
resulted in a standard known as ISO 3448, whose American equivalent was published as ASTM D2422 [2,7].
The ISO viscosity classification system consists of 18 grades, starting with ISO VG 2 and ending with ISO VG 1500 [6]. The numbers written in front of the ISO VG code indicate the kinematic viscosity of the industrial oil in rounded values. For example, the actual kinematic viscosity for an ISO VG 2 grade is 1.98 cSt or mm2/s, or ISO VG 1500 grade has a kinematic viscosity of 1650 cSt. There is a 50% difference between viscosity grades in ISO VGs. In other words, as the viscosity grade of the oil in the ISO system increases, the viscosity of that oil increases by half of the previous viscosity. This spacing is intended to make the difference between various grades of oil viscosity obvious and significant.
However, this grading has 4 imperfections:
I- There are oils whose kinematic viscosity at 40°C does not match any of the grades specified in this system, and even the upper and lower tolerances defined in the ISO system do not meet this gap [2,6]. For example, canola oil, which is used in the production of fireproof hydraulic oils in addition to cooking, has a kinematic viscosity of 38mm2/sec at 40°C. This makes canola oil undefinable in the ISO system. Because the viscosity of this oil is between ISO VG 32 and ISO VG 46 standard grades and none of them practically covering it [2].
II- The ISO system only deals with the kinematic viscosity of industrial oils at 40°C. There were two reasons for choosing this temperature point:
- 40°C is a good intermediate point between the two temperature points of the maximum oil operating temperature and the ambient temperature, and
- 40°C is one of the most important characteristics in determining the viscosity index.
Although the reasons for choosing this temperature point cannot be easily ignored, the choice of 40°C makes the ISO system unsuitable for industrial oils which intended to operate at low temperatures.
III- The ISO system does not mention the viscosity index of each of the oil grades defined. In other words, the ISO system user cannot distinguish whether the ISO VG 32 grade chosen oil is VI 30 or VI 200.
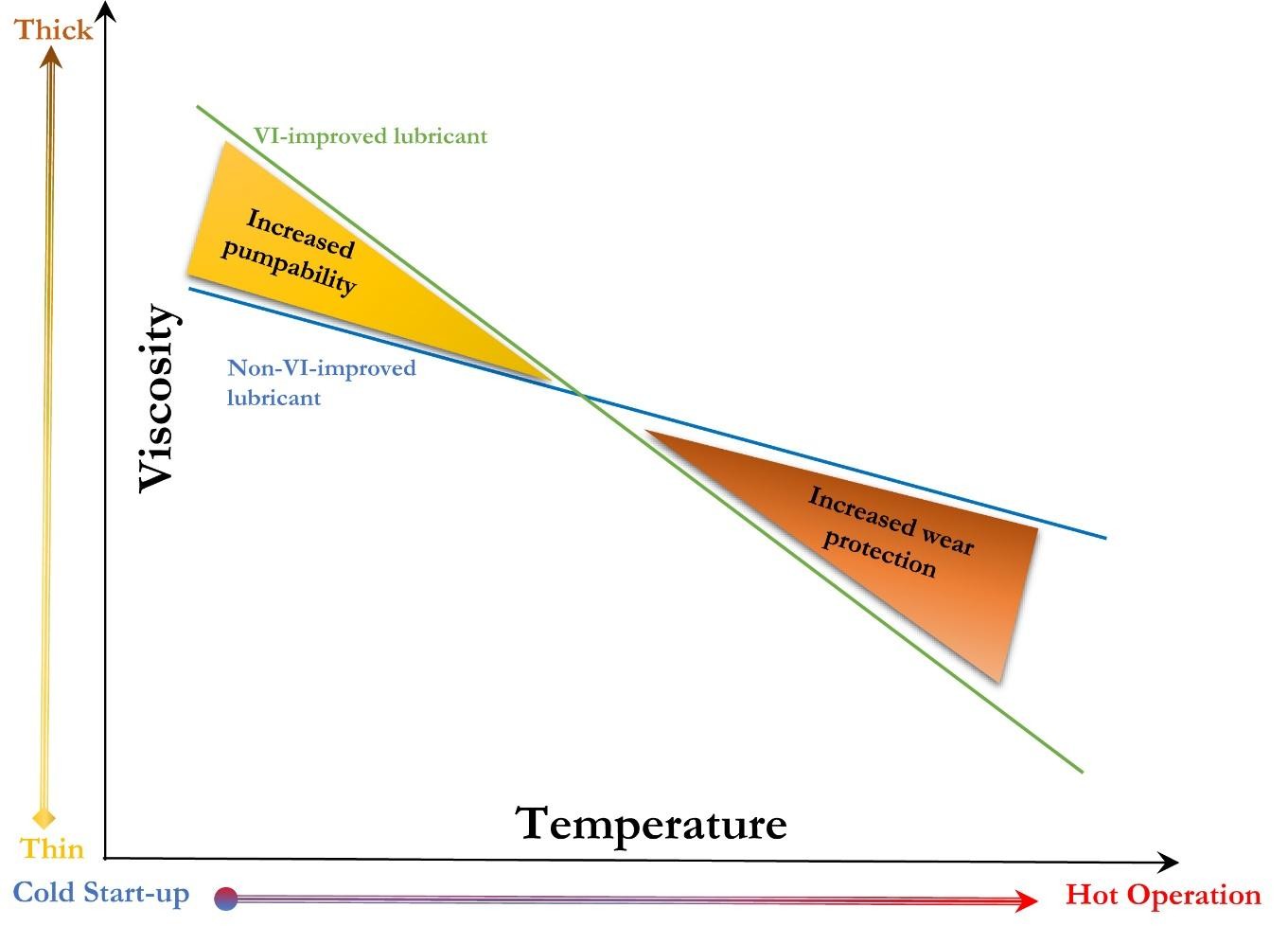
IV- Last imperfection mostly appeared in oil analysis: the ISO system is only dedicated to classifying the viscosity of new oils, and there was no space in its formulation for grading used hydraulic oils. In mining industry, when hydraulic oils get analyzed, new oil samples can be expressed based on this system (e.g. ISO VG 32). However, if the same hydraulic oil analyzed after working for certain period and its kinematic viscosity becomes, for example, 37mm2/s, its kinematic viscosity can no longer be expressed in the oil analysis report relying on the ISO system [6].
Nevertheless, the ISO system is simple, understandable, and rational. Although several viscosity classification systems have been introduced since then, it has still maintained its popularity [2].
Table 1 shows the classification system of industrial hydraulic oils based on two common standards ISO 3448 and ASTM D2422.
![Table 1-The ISO system [2,5-6].jpg](img/Ahmadreza-Aminian-ARTICLE-images-3.jpg)
3. GOST system
After years of using different kinds of hydraulic oils in general industries, in the 1980s the USSR decided to collaborate with western organizations in order to facilitate Russian-made mineral oils export. The then formed state organization for standardization in the USSR (called the GOST ) issued a standard with regard to introducing a classification system for mineral hydraulic oils based on their kinematic viscosity filed as GOST 17479.3 which can be assessed as what exactly the ISO system did.
![Table 2- The GOST system [9]](img/Ahmadreza-Aminian-ARTICLE-images-4.jpg)
When comparing tables 1 and 2, It can be concluded that the GOST system is completely modeled after the ISO system; with the difference that we no longer see the “midpoint” in the minimum and maximum range for each class of viscosity, and at the same time, the GOST system does not cover all types of viscosity classes as widely as the ISO system.
4. ASTM system
This system, which was introduced in 1997 to optimize the ISO classification system, defined in the ASTM D6080 standard and is dedicated to hydraulic oils and actually is based on the ISO system. Therefore, in the ASTM system, we see the use of the kinematic viscosity criterion at a temperature of 40°C. However, in the ASTM D6080 standard, an attempt has been made to complete the ISO system. In this way, in addition to the kinematic viscosity at 40°C, we see the addition of information about hydraulic oil, including cold tolerance grade, kinematic viscosity at 40°C after shearing, and viscosity index after shearing [2].
The ASTM oil viscosity classification system was developed specifically for industrial hydraulic oils and therefore has a more limited viscosity range. This system starts from ISO VG 5 and ends at ISO VG 150 (just like the GOST system). The hydraulic oil classification format in the ASTM system is shown in Figure 3:

The components of the hydraulic oil identification code shown in Figure 3 represent the following information, respectively:
- The two numeric characters xx that come after the ISO VG code indicate the kinematic viscosity of the new hydraulic oil at 40°C. Just like the same format as mentioned in the ISO system.
- The letter L in this coding system stands for Low-Temperature (Cold) and its purpose is to express the functional properties of hydraulic oil at low operating temperatures. Here, the intention is to show at what temperature the said hydraulic oil reaches a viscosity of 750cP in the Brookfield viscometer. This number is chosen for the viscosity of hydraulic oil in the cold, which is a critical point for the start-up of the hydraulic pump in the cold. Thus, each ISO VG grade in this system has a cold performance temperature range, which is obtained by extrapolating the temperature performance range of that grade from the viscosity of hydraulic oil at 40°C. The method of obtaining this cold temperature range is the same for each ISO VG grade: there is a range of viscosity changes (tolerance) , which is related to the maximum and minimum numbers with the viscosity index VI 100 (as default) and equal to the answer Viscosity equation with 750mPa.sec, the cold temperature range (maximum and minimum temperature points) of that oil can be reached. It is obvious that, according to the need, the viscosity index can be assumed from VI 100 times another number (higher or lower, depending on the quality of the hydraulic oil) and the temperature range can be obtained according to the VI calculation formula defined in the ASTM D2270 standard. For example, ISO L22 hydraulic oil has a cold temperature range of -15°C to -23°C.
- The two numerical characters zz represent the kinematic viscosity of the used hydraulic oil at 40°C after shearing. The criterion for determining this viscosity for used oil is the shearing test of hydraulic oil in a sonic oscillator for 40 minutes . This test method is defined in the ASTM D5621 standard .
- The two numbers in parentheses (VI) also represent the viscosity index of used oil after a 40-minute sonic shear test based on ASTM D5621 standard [2,6-7].
Table 2 shows the classification system of hydraulic oils based on ASTM D6080.
![Table 3: The ASTM system [2,6-7]](img/Ahmadreza-Aminian-ARTICLE-images-6.jpg)
Fig.4 gives an example:
![Figure 4: An example of the viscosity grade of hydraulic oil in the ASTM system [2]](img/Ahmadreza-Aminian-ARTICLE-images-7.jpg)
According to the interpretations presented in this section, the numbers shown in Figure 4 represent a hydraulic oil that, when not yet running (new), has a kinematic viscosity of ISO VG 32 at 40°C (according to tolerances shown in table 1), and has a cold performance grade of L22 (with the thermal range defined in table 3) and in the working state, it has a kinematic viscosity of 30mm2/s at 40°C and a viscosity index of VI 150.
Roller Bearing which works for 20 hours with the design load; At the end of the test, the kinematic viscosity of the new and used oil is measured and compared.
4. NFPA system
In 2002, the national power fluid association (NFPA) published a recommended practice as T2.13.13 to aid users with the selection of appropriate viscosity grades which was reproduced based on most of OEM pump and motor component manufacturers recommendations where one can find the minimum, maximum and optimal viscosity recommendations sorted by manufacturers’ pumps and motors. Then after, NFPA’s recommended practice provides the methodology to determine an appropriate fluid viscosity grade for the given pump and its presumed temperature operating range via two processes:
- TOW which graphically presents the usable temperature ranges for typical hydraulic ISO VG10~100 based on extrapolating mid-range ISO VGs with a VI of 100 to viscometrical targets of 13~860 cSt at startup.
- ALTOW which is more complex and used when an application not fall within the TOW ranges, or the pump’s recommended viscosity range be substantially different than the 13~860cSt. As a variation of the ASTM D 341, the ALTOW method assumes a VI of 100 for all oils.
The NFPA system of grading has two imperfections:
I- It did not take into consideration the probable shearing of multigrade fluids based on VI improvers and their consequent loss of viscosity. Thus, fluids susceptible to shearing might be misapplied in applications where the used-oil viscosity becomes too low.
II- Although the NFPA grading system works well for hydraulic fluids with VI > 100 [7], it needs even higher VI limits (min. VI of 160) for fluids intended for after-shearing conditions based on ASTM D5621 [2]. These sever conditions takes most of the hydraulic fluids out (especially the mineral-based and foreign-born fluids compared to what is producing in the USA).
Although the NFPA did not move forward after its recommended practice published in 2002 and then re-approved in 2015 and 2020, table 4 summarizes the NFPA system
trying to still utilize the well-known ISO VG nomenclature and being based on 100°C rather than 40°C kinematic viscosity after shearing via ASTM D 5621.
![Table 4: The NFPA system [2]](img/Ahmadreza-Aminian-ARTICLE-images-8.jpg)
5. Conclusion
The ISO system for viscosity classification is simple, rational, and popular. So that all the other systems came after were modeled based on the ISO (e.g. the GOST system). However, because of some imperfections especially regarding hydraulic groups of fluids, the ASTM system looks more complete and in-hand. Nonetheless, the author believes that the NFPA system will be even more applicable to hydraulic oils than the ASTM system after completion.
- American Society for Testing and Materials
- Society of Tribologists and Lubrication Engineers
- British Standard Institute
- Deutsches Institut für Normung = German Institute for Standardization
- Noteworthy, the STLE was known as ASLE at the time of the development of the above standard.
- ISO VG: ISO Viscosity Grade
- 750 cP = 750 mPa.sec (dynamic viscosity) equal to 860 mm2/s (kinematic viscosity) is the final tolerable limit of viscosity for the pump in start-up.
- See table 1
- This test is supported by engineering studies. There is a direct and undeniable relationship between the mechanical shearing of hydraulic oils due to frequent and continuous pumping with the simulated shearing in the sonic oscillator.
- Although this method is popular among many American OEMs, it is quickly being replaced by the CEC L45-A-99 KRL test method known as the Tapered Roller Bearing Test. This test method has gained more acceptance among OEMs around the world because of more realistic results. For this test, new oil is poured into the lubrication chamber of a Tapered.
- Temperature Operating Window
- ≈750 mPa.s
- Alternate TOW
6. References
In writing this article, in addition to personal experiences and observations, the following references have also been used, a short list of which is provided for the further study as follows:
- S. Herzog and T. Marougy , Determining Hydraulic Fluid Viscosity Requirements, Machinery Lubrication magazine (1/2007), Web article available at https://www.machinerylubrication.com/Read/974/hydraulic-oil-viscosity, accessed September 21st 2022;
- G. E. Totten and V. J. De Negri (Editors), B. G. Kinker, P. W. Michael, and T. S. Wanke, Handbook of Hydraulic Fluid Technology, 2nd Edition, CRC Press, ISBN 978-1-4200-8527-3, 2012, pp. 207-212;
- R. W. Bruce (Editor),J. B. Hannon , Handbook of Lubrication and Tribology, Volume II: Theory and Design, 2nd Edition, CRC Press, ISBN 978-0-4291-3737-2, 2012, pp. 31.1-31.15;
- S. Herzog, C. Neveu, D. Placek, The Benefits of Maximum Efficiency Hydraulic Fluids, Machinery Lubrication, 7/2005;
- S. Javalagi, S. R. Singireddy, Hydraulic fluid properties and its influence on system performance, Master’s degree project, Division of fluid and mechatronic systems, Department of management and engineering, LIU-IEI-TEK-A--12/01284—SE, Linköping Universitet, Tekniska Högskolan, 2012, pp. 8-19;
- P. W. Michael, S. N. Herzog, T. E. Marougy, Fluid Viscosity Selection Criteria for Hydraulic Pumps and Motors, National Fluid Power Association (NFPA), Technical Paper Series, I00-9.12, Presented at the International Exposition for Power Transmission and Technical Conference, 4-6 April, 2000;
- L. R. Rudnick (Editor), R. Lyer, T. Schimmel, and D. C. Placek, Synthetics, Mineral Oils, and Bio-Based Lubricants: Chemistry and Technology, 2nd Edition, CRC Press, ISBN 978-0-4291-0505-0, 2013, pp. 543-565;
- Exxon Mobil Corporation, Hydraulic Fluid Shear Stability, Technical Topic, HY8011SH, 2008;
- GOST 17479.3-85, Hydraulic oils. Classification & Designation, (in Russian).
About the Author
As the deputy of engineering & technical affairs in the field of rolling stock, Ahmadreza leverages more than two decades of experience directing engineering management and multinational challenges in technology transfer governance. Currently, as a professional in the lubricant analysis, his unique background as an aerospace, mechanical, and welding engineer serves him to be an international consultant in rolling stock, power plants, and rotating machinery. Contact Mr. Ahmadreza Aminian at araminian78@gmail.com.
Ahmadreza Aminian | Lubrication Expert | Iran