Challenges of lubricating greases in applications of Steel Production
Most of the many applications of lubrication in the steel industry are extremely challenging. Often there are roller bearings operating under high loads with exposure to contamination of water and dust along with radiation heat, vibration, and shock loads. In the following, three typical examples of rolling bearing lubrication in the steel industry will be discussed. These are:
- Bearings of rolling tables in hot and cold rolling mills
- Bearings of strand guiding rollers of continuous casters
- Non-continuously operated bearings, such as in cranes or converter main bearings
1.1 Bearings of Rolling Tables in Hot and Cold Rolling Mills:
Rolling tables are transportation units for solid steel products or semi-finished products. They are cascades of parallel rollers vertically in the direction of transportation of the goods lying on them. In rolling mills, they are found over the complete length. Since this results in a certain distance and a remarkable number of bearings, they are mostly lubricated by central lubrication systems. Therefore, the first requirement for the selected lubricant is its capability to be supplied by the central lubrication system. Furthermore, there are shock loads any time the steel is passing. Usually greases of sufficient base oil viscosities to ensure a viscosity ratio of κ> 1 are proven for these purposes. In cases of oil lubrication, the viscosity ratio should be several times higher, approximately κ≈ 4.
There is always a certain risk of contamination with dust and water. This refers especially to the cooling zone in hot rolling mills where the steel and the rolling table are flushed by an enormous amount of water. This water washes the oxides of the mill scale from the steel, and the ingress of this contaminated water will jeopardize the bearing life. Therefore, the proper sealing of the bearings is essential. In the common case of grease lubrication via a central lubrication system, the continuous re-lubrication provides sufficient sealing properties. This also requires that the lubricant is suitable to flow through the narrow pipelines of central lubrication systems without too much pressure loss, and not to exceed the maximum pump capacity. A procedure to assess this suitability and to calculate the required pressure of the pump has been presented with the Bechem Rheometer Curve [13]. To avoid excessive re-lubrication and to maintain proper sealing, the grease should have sufficient water resistance. A common method to assess the water washout characteristics of lubricating greases from bearings is the test according to DIN ISO 11009 [14]. In the corresponding test rig, water is sprayed on a running bearing, and the washout of grease is determined after weighing the dried bearing with the remaining grease afterwards.
In hot rolling mills, the first rolling tables after the exit of the furnace are not exposed to water but to strong radiation heat. This bears the risk of exceeding the temperature resistance of the grease, which may lead to softening resulting in leakages in some cases, or to hardening resulting in blockages of the bearing or, even more, of the pipelines of the central lubrication system in other cases. In both cases, the bearing is suffering from a lack of lubricant. Therefore, a lubricant with sufficient heat resistance has to be selected for these areas of the rolling tables.
For the lubrication of rolling tables, mostly greases are supplied via central lubrication systems. Another proven option is oil-air lubrication systems. In those systems, the bearings are connected to pipelines that provide constant airflow to the bearings, keeping them at a higher pressure level that saves them from the ingress of water and other contaminations. Additionally, a small amount of oil is dosed into the system and driven by the airflow to the bearings. Meanwhile, those systems are quite often found in the steel industry, since they have proven to work reliably. Compared to grease lubrication, however, the investment costs of oil-air systems are higher. Regarding the costs of operation, contradictory experiences were reported.
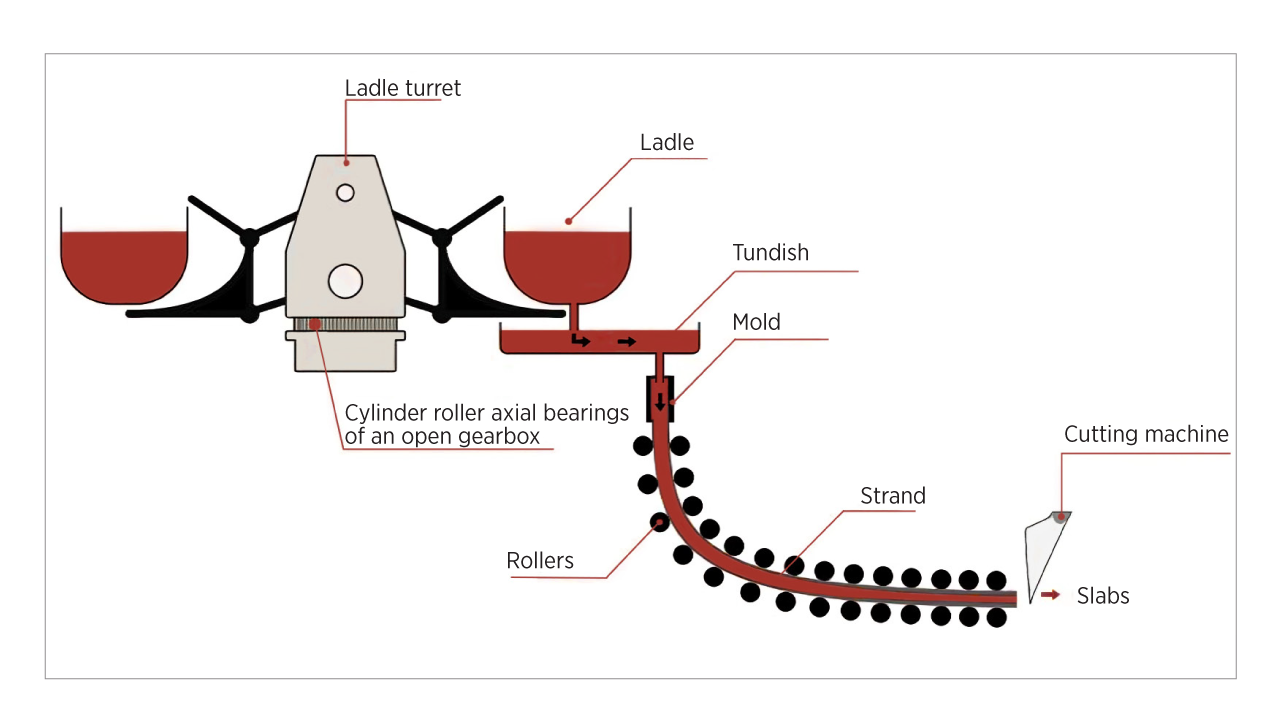
Fig. 1: Schematic view of a continuous casting line with a huge number of rollers
1.2 Bearings of Strand Guiding Rollers in Continuous Casters:
In continuous casters, especially slab casters, the strand is guided by a huge number of rollers with two or more bearings each, as is illustrated in Fig. 1. The lubrication of these strand-guiding rollers in continuous casters is a key problem of maintenance in the steel industry. Everything that has been discussed for rolling table lubrication in Section 1.1 refers to the lubrication of strand-guiding rollers in continuous casters, too. However, the problem is even more difficult since the described problems of water contamination, including abrasive particles, and exposure to heat radiation may occur for the same bearing.
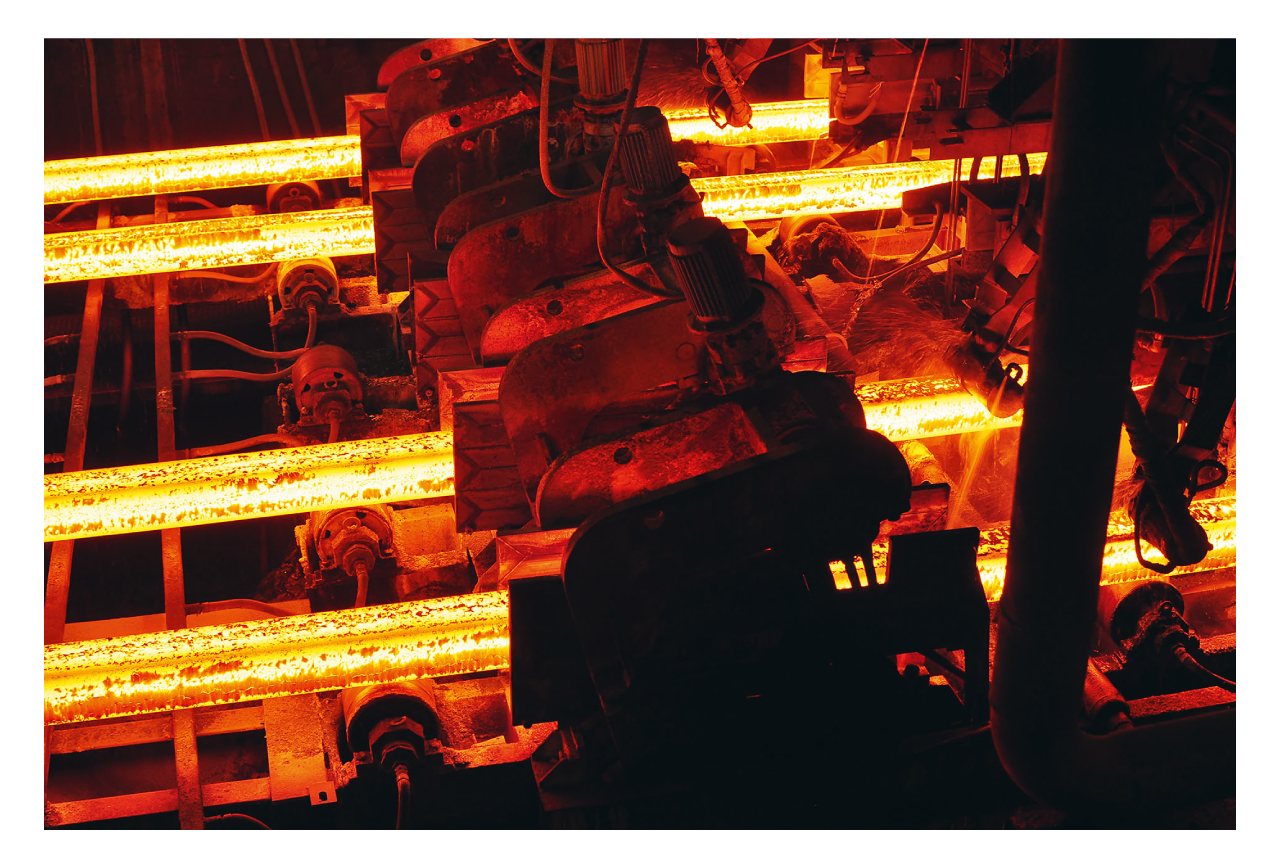
Fig. 2: View on strand guiding rollers of a billet caster in operation
Depending on the operation of the caster, the bearing may be flushed with high amounts of water for a certain period, and at another time there may be a lack of cooling water and an extreme exposure to radiation heat. Even if there is sufficient cooling for the bearing, the lubricant may suffer from radiation heat inside the pipelines of the central lubrication systems. Fig. 2 shows the strand-guiding rollers of a billet caster in operation and gives an impression of the severe conditions of the operation. Just like the bearings of rolling tables, the bearings of strand guiding rollers in central lubrication systems are mostly connected to central lubrication systems. Again, mostly grease lubrication systems are applied, but also oil-air lubrication systems are often found nowadays.
Another special challenge of the lubrication of strand guiding rollers results from their extremely low rotational speed of mostly n< 10 min-1. The average bearing diameter will mostly be dm < 200 mm. Therefore, according to Eq. 6, a rated viscosity of ν1> 470 mm²/s is required to achieve a lubricant film parameter of Λ> 1 that provides minimum wear. Considering a temperature ϑ > 80°C of the bearing, which is definitely not unrealistic, even an extremely high viscous mineral oil of ν = 1200 mm²/s at ϑ = 40°C will result in a viscosity ratio of κ< 0.28. Usually, such high-viscous lubricants are not applied because they will cause serious problems with re-lubrication. In the practice of strand guiding rollers, typically (base) oil viscosities of 100 < ν< 500 mm²/s at 40°C are applied, and the viscosity ratio is to be expected in a range of 0.02 < κ< 0.2. According to Eq. 9, this refers to a range of the lubricant film parameter of 0.05 < Λ< 0.29. That means the surfaces in contact are hardly separated, metal-to-metal contact is happening, and wear occurs. Under such a condition, the lifetime of the bearings is usually reduced to 10 or max. 20% of the basic rating life L10. However, since the basic rating life of L10 is given in a million revolutions and the rotational speed n is extremely low, this still results in a sufficient lifetime given in hours of operation as far as fatigue damages are concerned.
Nevertheless, due to the extremely thin lubrication film and the fact that these bearings are mostly roller bearings, they are very prone to contamination with even small particles that can hardly escape from the line contact of the rollers and will cause extensively high local stresses that may lead to damages. Therefore, sealing the bearings from contamination with hard and abrasive particles is the most important topic of the lubrication of the bearings of strand guiding rollers in continuous casters.
1.3 Non-continuously Operated Bearings such as in Cranes or Converters Main Bearings:
Apart from those bearings with extremely low rotational speed, as discussed above, there are also some bearings that are non-continuously operated. Typical examples in the steel industry are bearings in cranes or converter main bearings. As discussed before, fluid lubrication of oils and greases is based on the movement of the surfaces. Any time non-continuously operated bearings stop rotation, the surfaces get into metal-to-metal contact. Without any further movement of the bearing, there is, theoretically, no shear stress and, therefore, no wear. But even during stoppages, vibrations may lead to a micro-oscillation of the bearing. These movements may sometimes lead to damage. The above-described phenomenon is discussed under the keyword false-brinelling. This wording is rather common but confusing at the same time. This damage does not result from an indention only but rather more from shear stresses caused by micro-movements hindering the replenishment of lubricant [15]. So far, no common theory on how to avoid the so-called false-brinelling damages has been found. Depending on the application, different strategies have prevailed. Generally, it has been found that oils or greases of low consistency and high oil separation are beneficial. Furthermore, solid lubricant particles as an additive of grease and, in rare cases, oils have proven to be helpful. Finally, special additives or thickeners providing tribo-layers have shown positive effects.
Developments:
In 1942, Earle [16] had his invention of a lubricant containing lithium soaps protected by a patent. Since then, greases thickened by lithium soap or lithium complex soap have become most common for the lubrication of rolling bearings, and they are still the dominant lubricant for this purpose. Sometimes lithium soaps are found in combination with calcium soaps. Furthermore, aluminium (complex) soaps and barium complex soaps are applied for rolling bearing lubrication. During recent decades, calcium sulfonate complex soap greases have become popular since they offer some unique properties with respect to water resistance, oil separation, and aptitude for the food industry. Recently, this new concept has substituted lithium soaps in many rolling bearings. Generally, soap thickeners have an upper-temperature limit of roughly 120 to 150°C; aluminium complex soaps and calcium sulfonate complex soaps may be applied even at slightly higher temperatures; simple calcium soaps only up to 80°C. Urea thickeners are non-soap thickeners invented for high-temperature applications at roughly 150 to 200°C a few decades ago. Depending on the base oil, some products may even be applied above 200°C. Soon it was observed that urea thickeners are resistant to water and many chemicals, which offers outstanding benefits in rough applications, such as heavy industry. Meanwhile, it appeared that this concept offers unique options for basically all applications. This refers to lifetime lubrication in roller bearings with line contact, too, which was doubted in the past. Modern urea greases have shown outstanding performance in high-speed and low-noise applications. For extremely high temperatures above 200°C, thickeners of polytetrafluoroethylene (PTFE) are available, especially when they are based on perfluoropolyether (PFPE) oils. However, these greases are very expensive. For the minority of oil-lubricated rolling bearings, standard circulating and gear oils have been applied for a long time. Mostly mineral oils are applied, but synthetic oils have gained more and more importance over the years. This refers especially to polyalphaolefines (PAO) and polyglycol. Lately, bio-based oils and ester oils in general are requested for some applications. All this refers to the base oils of the beforementioned greases, too. Still, anti-friction coatings are hardly found in rolling bearing lubrication, even though they may be a solution for extreme conditions such as ultra-high temperatures above 300°C or vacuum, where any fluid will evaporate. But also for other applications, a combination of anti-friction coating and grease was found to deliver outstanding results in the latest research. The newest development is coatings where the solid lubricant particles are substituted by microcapsules of a few micrometers. Under the load and the shear stresses in between the surfaces in contact, the capsules in the boundary layer will break, giving off the fluid lubricant they have contained.
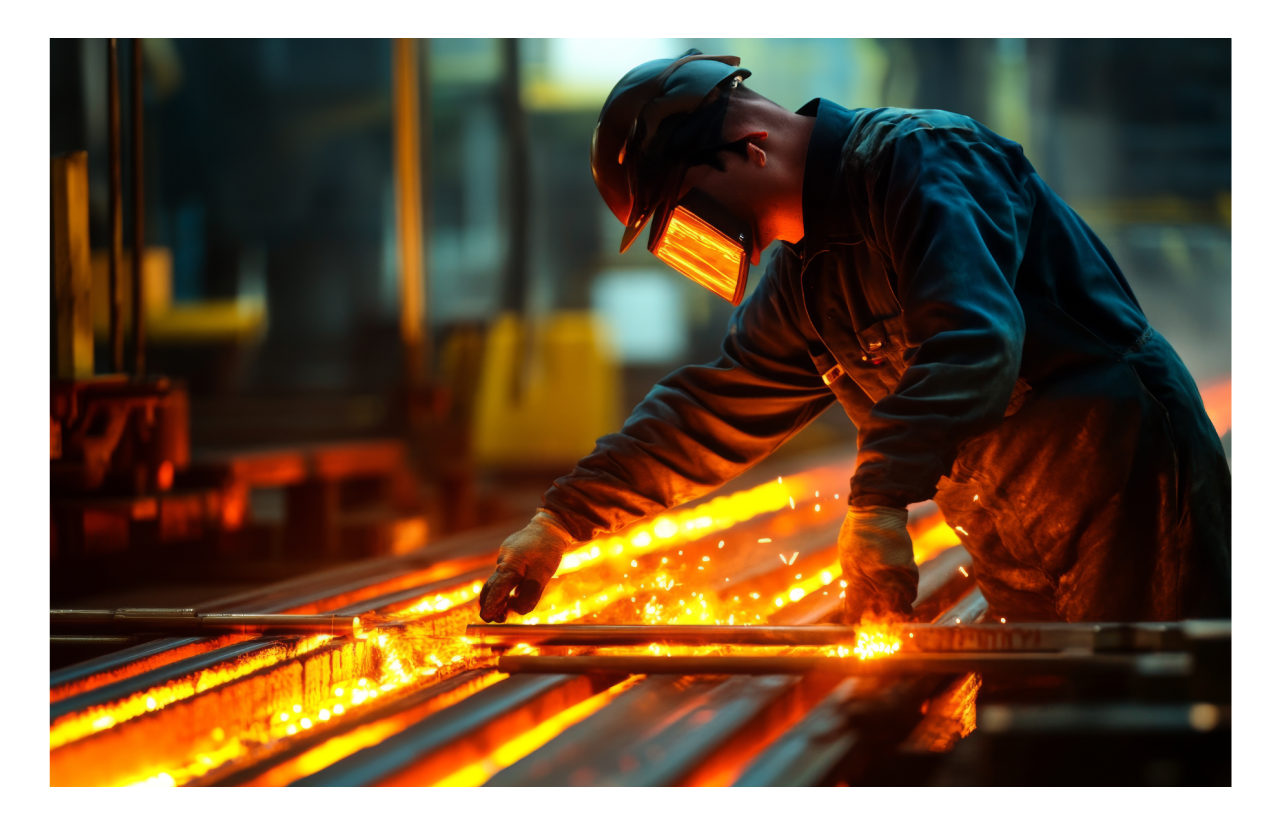
References
- Berg- und Hüttenmännische Monatshefte, Lubrication of Rolling Bearings by Frank Reichmann SKF: Lagerschäden vermeiden und dadurch viel Geld sparen. https://evolution.skf.com/de/golden-opportunities (Created 8 June 2011). Accessed 30 Nov 2021
- Engel, L., Winter, H.: Wälzlagerschäden. Antriebstechnik 18(3), 71–74 (1979)
- Schaeffler Technologies: Wälzlagerpraxis: Handbuch zur Gestaltung und Berechnung von Wälzlagerungen, 4th edn. Vereinigte Fachverlage, Mainz (2015)
- Wisniewski, M.: Elastohydrodynamische Schmierung. Handbuch ´ der Tribologie und Schmierungstechnik, vol. 9. expert, Renningen (2000)
- Tallian, T.E., et al.: Lubricant films in rolling contact of rough surfaces. ASLE Trans. 7(2), 109–126 (1964)
- Heemskerk, R.: Ehd lubrication in rolling bearings. Tribologia e Lubrificazione, vol. XV. (1980)
- DIN ISO 281: “Wälzlager – Dynamische Tragzahlen und nominelle Lebensdauer”, DIN Deutsches Institut für Normung e.V., Beuth Verlag GmbH, 2010
- Dubbel: Taschenbuch für den Maschinenbau, 16th edn. Springer, Berlin, Heidelberg, New York, London, Tokyo (1987)
- Lugt, P.M.: Grease lubrication in rolling bearings. John Wiley & Sons (2013)
- Schmitt, H., Ganz, M., Beck, J.: Seminar Wälzlagerauslegung – Rechnerische Lebensdauer und konstruktive Gestaltung. Industrial Market, Regional Sales and Services CWE. SKF (2013)
- Schaeffler: Rolling bearings. Schaeffler Technologies (2014)
- SKF: “Hauptkatalog”, SKF Gruppe, November 2012
- Reichmann, F., Tönsmann, A.: Bestimmung von Bechem-Rheometerkurven für Schmierfette aus Versuchsergebnissen mit einem Rotationsviskosimeter. Tribol. Schmierungstech. 62(1), 60–67 (2015)
- DIN ISO 11009: “Bestimmung der dynamischen Wasserbeständigkeit von Schmierfetten”, DIN-Normenausschuss Materialprüfung (NMP), Beuth Verlag GmbH, September 2019
- Grebe, M.: False-Brinelling und Stillstandsmarkierungen bei Wälzlagern. expert, Renningen (2017)
- Earle, C.E.: Lubricating composition. United States Patent 2,274,674. Washington, D.C. (1942) Publisher’s Note. Springer Nature remains neutral with regard to jurisdictional claims in published maps and institutional affiliations
- Mattern, T.: Herausforderungen bei der Schmierung von Anlagen in der Stahlindustrie, Schmierstoffe und Schmierung issue 2/2023
About the Author
Tim-Oliver Mattern is a seasoned industry expert with over 30
years of experience in the metal sector, including 22 years in
lubricant marketing, sales, and business development. His specialities
include lubricant sales, marketing, and technology, as well as
extensive grease knowledge and an in-depth understanding of various
industries such as power, metals, mining, paper, automotive, and
automotive components. Currently, Mr. Mattern heads the Core Market
Steel and Global Steel Team at Carl BECHEM GmbH in Hagen, Germany.
Contact Mr Tim Oliver Mattern at mattern@bechem.de
Mr. Tim-Oliver Mattern
Head of global lubricants business – Steel Industry & Head of global
steel team | Carl BECHEM GmbH