Enhancing Sustainability and Efficiency in Steel Production Through Advanced Lubrication Strategies
Introduction
The global iron and steel market, valued at approximately $1,600 billion, is experiencing a steady growth rate of 3.8% CAGR. As steel production continues to drive the economies of numerous countries, there is an increasing push towards sustainability. This shift is not only about adopting green technologies but also about enhancing operational efficiency across the value chain. One critical area often overlooked in this quest for sustainability is the role of efficient lubrication in machinery. Proper lubrication can substantially reduce operational costs, increase equipment lifespan, and contribute to overall sustainability.
Economic Impact of Inadequate Lubrication
Sustainability in steel production isn't just about adopting green solutions; it's also crucial to implement more efficient systems that enhance productivity through a better understanding of machinery tribology. According to Global Industry Analysts (GIA), the annual global cost of inadequate lubrication in industrial machinery is estimated to be around $100 billion, a cost that could be significantly reduced. Studies indicate that improper lubrication accounts for 30-50% of equipment failures in industrial settings. The National Lubricating Grease Institute (NLGI) reports that unplanned downtime due to equipment failure can cost between $500 and $1,000 per hour, depending on the industry and machinery involved.
Sustainability Through Efficient Lubrication
Sustainability in steel production extends beyond the adoption of green manufacturing processes. It encompasses the implementation of efficient systems that enhance productivity and reduce operational waste. In integrated steel plants, lubrication challenges are significant due to the diverse operating environments and equipment types. These environments range from high temperatures and heavy loads to dusty and corrosive conditions. Effective lubrication practices can play a crucial role in mitigating these challenges and driving sustainability.
Lubrication Challenges in Steel Plants
An integrated steel plant consists of several key process groups, including Iron Making, Steel Making, Rolling and Finishing, and Auxiliary Units. Each of these groups presents unique lubrication requirements due to differing operating conditions:
- Iron MakingEquipment operates under high temperatures(1,600°C-2,300°C) , abrasive dust, and corrosive environments. Typical applications include raw material blending and coke ovens. Lubricants must withstand extreme conditions and protect against wear and corrosion.
- Steel Making:This group includes LD Furnaces and continuous casters, where equipment faces high temperatures (1,600°C-1,800°C) and abrasive conditions. The lubricants used here need to be highly resistant to oxidation and thermal degradation.
- Rolling and Finishing: Equipment such as Hot Strip Mills and Cold Rolling Mills operates under high impact loads and high speeds. Lubricants must handle high temperatures and moisture ingress while maintaining efficient performance.
- Auxiliary Units: These units support the main processes and have varied lubrication needs based on their specific functions and conditions.
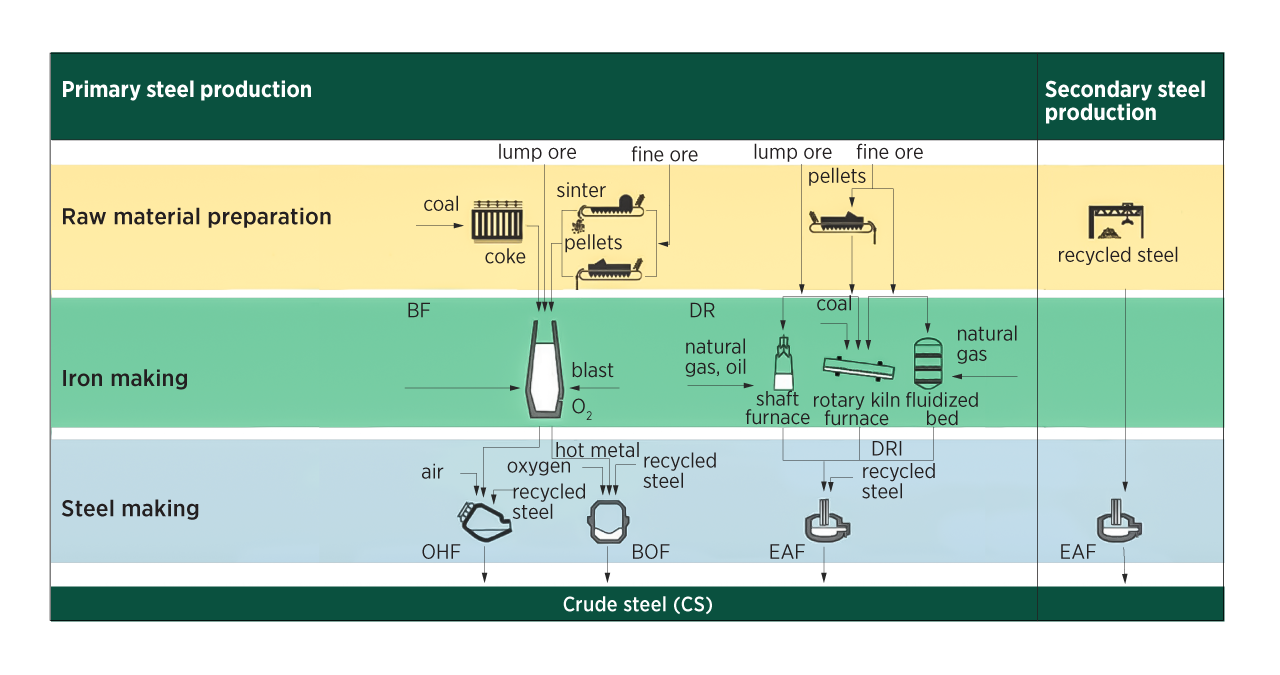
Cost Implications and Maintenance
Lubrication directly impacts maintenance costs and equipment reliability. Maintenance costs in steel plants are approximately $ 20 per tonne of crude steel, accounting for 10-15% of the total production cost. Proper lubrication can reduce these costs by preventing breakdowns and extending equipment life. While high-quality lubricants may slightly increase upfront costs, the long-term benefits include reduced downtime, fewer replacements, and optimized maintenance expenses.
Lubricant Selection Criteria
Selecting the right lubricant involves considering both engineering requirements and service conditions. Engineering requirements include factors such as load, speed, and temperature, while service conditions address factors like moisture and dust ingress. Lubricant selection should align with these parameters to ensure optimal performance and protection.
- Base Oils: The shift from Group I to Group II base oils reflects advancements in lubrication technology. Group II base oils offer superior oxidation stability and thermal performance, which are essential for steel plant applications.
- Additives:Additive packages are critical for addressing specific lubrication challenges. These include rust inhibitors, anti-oxidants, and anti-foaming agents tailored to the operational demands of steel plant equipment.
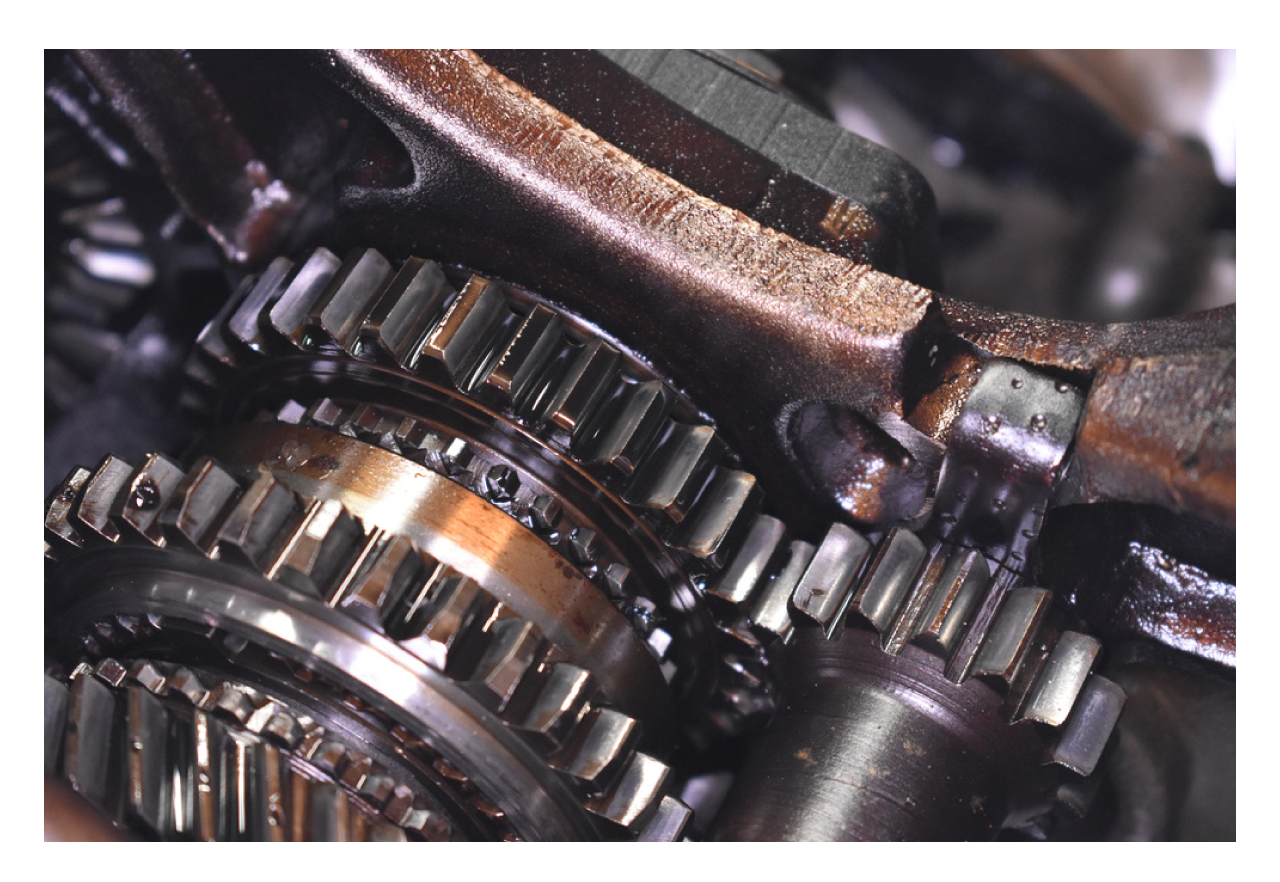
Operational Efficiency and Equipment Life
The effectiveness of lubrication directly correlates with equipment reliability and productivity. Cleaner lubricants and efficient lubrication systems enhance equipment life and reduce maintenance needs. For example, increasing hydraulic fluid cleanliness can extend pump life by a factor of 50 and reduce bearing failures by up to 90%. Implementing condition monitoring programs further optimizes lubricant usage and ensures consistent equipment performance.
Conclusion
Efficient lubrication is a cornerstone of sustainability and productivity in steel production. By addressing lubrication challenges and selecting appropriate lubricants, steel plants can enhance operational efficiency, reduce costs, and contribute to overall sustainability goals. Investing in high-quality lubricants and adopting advanced lubrication practices not only supports environmental objectives but also drives economic benefits through improved equipment reliability and reduced maintenance costs. As the steel industry continues to evolve, integrating robust lubrication strategies will be pivotal in achieving both sustainability and operational excellence.
About the Author
With over 13 years of experience in the steel sector, Soumya Ranjan
Pradhan is an expert in technology and sales, driving innovation and
growth. An alumni of IIM Kozhikode, he blends advanced leadership
skills with a strong technical foundation. Passionate about enhancing
operational efficiencies and sustainability, Soumya Ranjan is
dedicated to shaping the future of these critical industries through
collaboration and strategic insights. With his experience in the
industry, Soumya Ranjan has been a part of many successful projects.
His knowledge and insights are commendable and worth hearing about.
You can reach Mr. Pradhan at soumyaranjanpradhan85@gmail.com
Soumya Ranjan Pradhan
Head-Project Sales & Approvals | Maruti Ispat & Energy Pvt Ltd