Powering Mining Success: The Role of Lubrication Solutions in Optimizing Operations
In this article, we will explore the vital role of lubrication in the mining industry, the challenges faced in choosing the right lubricants, including energy-efficient, synthetic, and biodegradable speciality lubricants, and how modern lubrication technologies and practices, including digital transformation, are evolving to meet the unique needs of this sector. From heavy-duty mining trucks to drilling rigs, lubrication is the unsung hero that keeps operations running smoothly.
The mining sector is fundamental to the global economy, driving the extraction of minerals and natural resources. The mining industry is under intense pressure to maximize profitability, a challenge that requires ensuring the reliability of its machinery and equipment. In this context, lubrication plays a critical role in maintaining the reliability of these systems, ensuring optimal performance, and minimizing downtime. Thereby, the lubrication solution takes one of the lead roles in the mining industry, as the global mining lubricant market size stood at USD 2,255.3 million in 2023. It is further projected to exhibit a Y-O-Y growth of 4.7% in 2024 and reach USD 2,340.5 million in the same year. Surging at a CAGR of 5.4% between 2024 and 2034, demand for these lubricants is estimated to reach USD 3,960.2 million by 2034.
Also, the mining industry is one of the most demanding sectors, with operations often occurring in remote and
harsh environments. Whether it is underground excavation, surface mining, or transporting materials, machinery
and equipment are subject to extreme conditions, including heavy loads, high temperatures, and dust. In such a
high-stakes industry, machinery uptime and efficiency are critical to maintaining productivity and safety. This
is where lubrication solutions come into play. Proper lubrication not only ensures optimal performance and
durability of mining equipment but also helps prevent costly breakdowns, reduce maintenance costs, and improve
operational safety.
Another challenge in the mining sector is to address the consumption of energy, as the total energy consumption
of global mining activities, including both mineral and rock mining, is estimated to be 6.2% of the total global
energy consumption. 40% of the consumed energy in mineral mining (equivalent to 4.6 EJ annually on a global
scale) is used for overcoming friction. In addition, 2 EJ is used to remanufacture and replace worn-out parts
and reserve and stock up spare parts and equipment needed due to wear failures. The largest energy-consuming
mining actions are grinding (32%), haulage (24%), ventilation (9%), and digging (8%).
The total estimated economic losses resulting from friction and wear in mineral mining are, in total, 210,000
million Euros annually, distributed as 40% for overcoming friction, 27% for the production of replacement parts
and spare equipment, 26% for maintenance work, and 7% for lost production.
By taking advantage of new technology for friction reduction and wear protection in mineral mining equipment,
friction and wear losses could potentially be reduced by 15% in the short term (10 years) and by 30% in the long
term (20 years). In the short term, this would annually equal worldwide savings of 31,100 million euros, 280 TWh
energy consumption, and a CO2 emission reduction of 145 million tonnes. In the long term, the annual benefit
would be 62,200 million euros, 550 TWh less energy consumption, and a CO2 emission reduction of 290 million
tonnes.
One of the potential new remedies to reduce friction and wear in mining operations is the employment of
Speciality and high-tech lubrication solutions including Energy Efficient Lubrication Solutions apart from using
improved metallurgy in equipment and machinery which can impart superior strength and hardness properties, more
effective surface treatments, high-performance surface coatings, and innovative designs of various sub-parts
viz., gearboxes, engines, shovels, shields, jaws, chambers, seals, bearings, conveyor belts, pumps, fans,
hoppers and feeders as each unit and sub-units need more improvement and innovation and usage of latest
Technology which ultimately aiming at reduction in wear & friction leading to reduction in maintenance cost at
large as the maintenance costs in mining companies comprise a considerable portion of the total cost of
operation.
The mining sector has been posing major challenges to lubrication for years, as proper lubrication is critical
for not only optimal performance but also the reliability and efficiencies of the equipment & machinery. As the
mining industry involves heavy-duty operations entailing the employment of heavy equipment and machinery, viz.,
draglines, excavators, shovels, haulage and transportation equipment, drilling equipment, etc., effective
lubrication becomes inevitable.
The mining industry relies on a wide range of equipment and machinery for various processes such as exploration,
extraction, transportation, processing, and reclamation.
Let’s briefly understand the main categories of equipment and machinery employed in the mining industry.
Exploration and Drilling Equipment
● Core Drilling Rigs: These rigs are used for geological exploration to sample materials below the
surface.
● Rotary Drills: These are required for drilling large-diameter holes in hard roc
● Percussion
Drills: Utilized for drilling blast holes.
● Sonic Drills: Used for geotechnical surveys and environmental assessments.
● Mud Pumps: For circulating drilling fluid during drilling.
● Blast Hole Drills: Used for drilling holes in preparation for blasting in mining operations.
Excavation Equipment
● Excavators: Large machines used to dig and move earth and rock.
● Backhoes: Smaller excavators for digging, lifting, and material handling.
● Front-End Loaders: Used to load materials onto trucks or transport and move bulk material.
● Shovels: Large electric or diesel-powered machines used for digging and scooping material.
● Draglines: Large machines used for overburden removal in surface mining.
● Bucket Wheel Excavators (BWEs): Large continuous mining machines for extracting minerals from
large, open-pit mines.
Crushing and Screening Equipment
● Jaw Crushers: These crushers are used for primary crushing of large rocks.
● Cone Crushers: Used for secondary and tertiary crushing to reduce material size.
● Impact Crushers: Used for softer materials that require less force to crush
● Gyratory Crushers: Used in large-scale mining for crushing large amounts of ore.
● Roll Crushers: Used to crush ores or minerals that are soft and medium-hard.
● Vibrating Screens: For screening crushed material to separate it by size.
● Grizzly Feeders: For separating coarse materials from finer materials.
Conveying Equipment
● Conveyor Belts: Used for transporting mined material from one point to another.
● Bucket Elevators: For vertically transporting material.
● Radial Stackers: To stack material in large piles in stockpiles.
Material Handling Equipment
● Forklifts: For lifting and transporting materials over short distances.● Cranes: For lifting and moving heavy machinery or equipment.
● Hoists: Used for lifting loads vertically.
Blasting Equipment
● Explosives: Used for breaking rock in mining operations.
● Blasting Machines: Equipment used to detonate explosives safely.
● Detonators: Devices used to trigger explosions in blast holes.
● Blast Mats: For controlling fly rock during blasting operations.
● Shotfirers: These professionals are responsible for blasting operations.
Drilling and Blasting Systems
● Down-the-Hole Drills (DTH): Specialized drills that drill through rock in preparation for blasting.
● Hydraulic Drills: Drills used in hard rock mines, particularly for blast hole drilling.
Haulage and Transportation Equipment
● Dump Trucks: Heavy-duty vehicles for transporting large amounts of material.● Articulated Haulers: Trucks used for hauling material in rough terrains.
● Loaders: Machines for moving and loading material into trucks.
● Haul Trucks: Large trucks used to transport ore or overburden.
● Rail Haulage Systems: Used in some mining operations for transporting materials via rail.
● Tippers: Vehicles with an open body used to carry loose materials.
Processing Equipment
● Ball Mills: For grinding ore into a fine powder.● Rod Mills: Used in grinding materials into smaller sizes.
● Flotation Cells: For separating minerals based on differences in their surface properties.
● Thickeners: Used to separate solids from liquids in mineral processing.
● Leaching Equipment: For extracting metals from ore using chemical solutions.
● Gravity Separators: Used for separating materials based on their density.
● Magnetic Separators: For separating magnetic minerals from non-magnetic ones.
● Hydrocyclones: Used for classification and separation in mineral processing.
● Shaking Tables: For separating minerals by density and particle size.
Ventilation Equipment
● Ventilation Fans: Used for circulating fresh air through mines and removing harmful gases.● Air Scrubbers: Used to clean the air of harmful dust and gases.
● Underground Ventilation Systems: Provide airflow to underground mining operations.
Pumping Equipment
● Water Pumps: To manage water flow and dewatering of mines.● Slurry Pumps: Used for handling liquid mixtures of water and ore.
● Sump Pumps: For removing water that accumulates in mine shafts.
● Pneumatic Pumps: Used in various mining applications to pump fluids.
Mining Support and Auxiliary Equipment
● Bolting Machines: For securing mine roofs and ensuring structural integrity.● Roof Support Systems: To prevent cave-ins and support the mine shaft.
● Ground Support Systems: Various mechanical systems used to stabilize mined areas.
● Exploration Samplers: For collecting samples during the exploration phase.
● Grout Plants: Used for injecting grout to stabilize mining tunnels.
● Underground Mining Carts: Used for transporting ore or waste in tunnels.
Underground Mining Equipment
● Continuous Miners: Machines used for cutting rock and ore continuously in underground mining.● Longwall Miners: For mining large amounts of coal and ore in long horizontal panels.
● Room and Pillar Mining Equipment: Used for mining coal or ore in a room and pillar system.
● LHD (Load-Haul-Dump): A machine used to load, haul, and dump mined material in underground mining.
Safety and Health Equipment
● Gas Detectors: For monitoring air quality and detecting hazardous gases in underground mining.
● Personal Protective Equipment (PPE): Hard hats, gloves, respirators, hearing protection, etc.
● Escape Chambers: Safe rooms in case of emergency for miners to retreat to during a disaster.
● Fire Suppression Systems: Installed in mining vehicles or equipment to prevent fires.
● First Aid Kits: For medical emergencies.
● CCTV and Surveillance Systems: Used for monitoring mining operations for safety purposes.
Waste Management Equipment
● Tailings Dams: Used to store by-products of the mining process.● Sludge Tanks: For storing and processing mining waste.
● Waste Rock Handling Equipment: To manage non-valuable rock removed during mining operations.
Reclamation and Rehabilitation Equipment
● Dozers: For regrading and reshaping the land during the reclamation process.● Compactors: For compacting soil and materials.
● Hydroseeders: For seeding and planting vegetation on reclaimed mine sites.
● Topsoil Spreaders: For spreading soil over reclaimed areas.
● Process Chart for Coal Mining
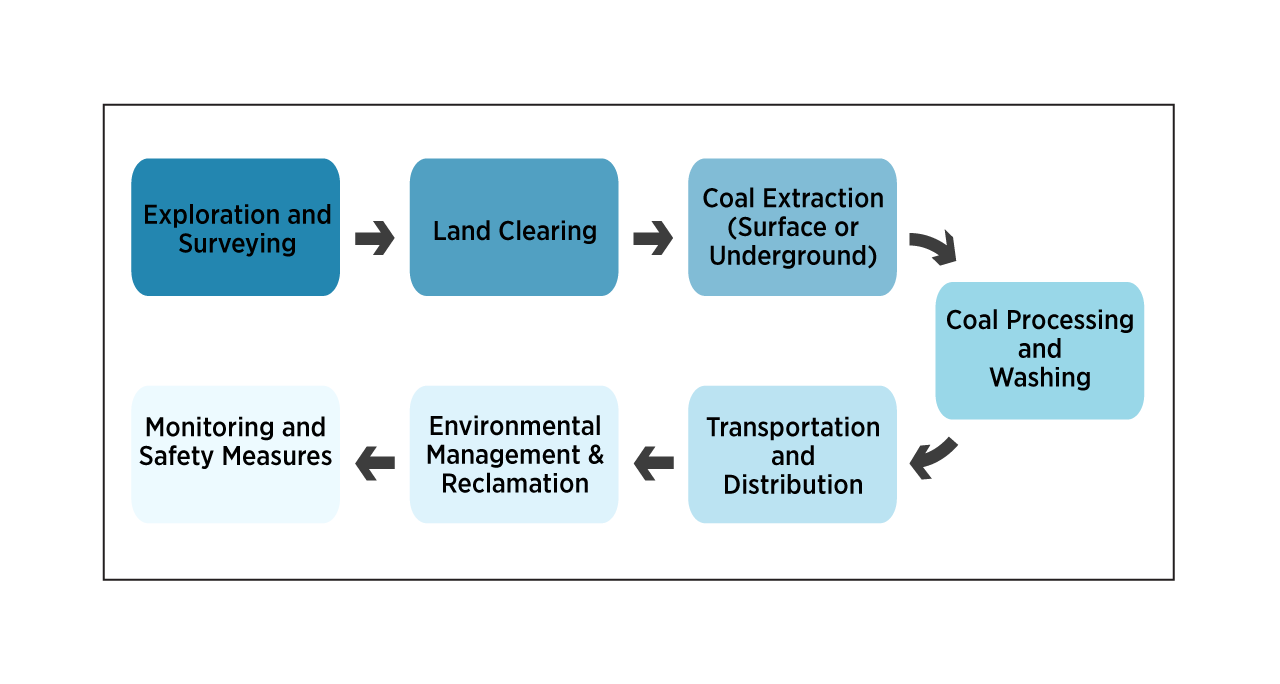
Key Operating Parameters in the Mining Industry
The mining industry is inherently demanding, with machinery subjected to harsh operating conditions such as
high temperatures, extreme pressures, heavy loads, and dust-laden environments. Given the scale of operations
and the often-remote locations of mining sites, ensuring the proper functioning of equipment is crucial for
minimising downtime, optimizing performance, and extending the life of valuable assets. At the heart of this
process is effective lubrication. Lubricants reduce friction, prevent wear, and protect vital components of
machinery from damage.
To achieve optimal performance, it isn’t enough to simply apply any lubricant. In the mining industry,
lubrication solutions must be tailored to the unique challenges each machine faces. This involves carefully
considering key parameters such as viscosity, load-bearing capacity, temperature resistance, and contamination
control.
The essential parameters that govern lubrication in the mining industry and understanding these factors is vital
for maximizing the efficiency, reliability, and safety of mining equipment.
The key operating parameters in the mining industry include heavy loads and high temperatures coupled with harsh
environments, which necessitate the employment of not only better lubricants but also the best in class, which
can withstand not only challenging parameters but also render high effectiveness and efficiencies to the system.
Another challenge lies in the selection of the right lubricants, including the right application techniques.
Apart from the above, the more important job of lubrication in mining lies in formulations that should be human-
and environmentally friendly to withstand these tough challenges. Many lubricant formulators use environmentally
friendly ingredients.
Challenges of Lubrication in the Mining Industry
To better understand the importance of lubrication in mining operations, let's first examine the key challenges faced by lubricants in this sector.
● Harsh Environment: Environments in any mining operations are very demanding, be it coal mining, iron ore mining, or any other mining operations, as it is full of dust and contaminants, which are very detrimental to lubricants.
● Heavy Loads – Mining activities often involve heavy loads, requiring the use of high load-bearing lubricants and greases, typically designed with high weld load or Timken load conditions.
● Application areas: Another challenge lies in application areas, as most of the equipment is huge and heavy, like draglines, shovels, etc., and some of the application areas are difficult to reach to do the proper lubrication at regular intervals.
● Moisture: Moisture is also injurious to lubricants, affecting the health of the equipment and machinery, and it is very common in mining areas.
● Temperatures: Mines are exposed to erratic temperatures that can degrade lubricants, posing another challenge to lubricant solution providers.
● Proper Monitoring and Conditioning: Due to the remote locations of mining areas and their accessibility, it becomes difficult to properly monitor mining equipment and machines like draglines, shovels, excavators, dumpers, etc., and it creates a tough job to make regular lubrication and maintenance. For instance, one of the Coal India subsidiaries, BCCL, operates 36 coal mines, which include eleven underground, sixteen open cast, and nine mixed mines in the year 2020. BCCL also runs eight coal washeries.
● Centralised Control: Another administrative issue can be the overall control of these mining areas, as they are normally far spread and are in remote locations, and their accessibility is a big issue, which can make regular lubrication and maintenance more challenging, and streamlining the lubrication solutions becomes another tough task for administration.
● Health and Environmental Concerns: Today, human health is of utmost significance, and it is the biggest challenge for lubricant providers to exclude the carcinogenic and toxic ingredients in the lubrication solution without losing the effectiveness of lubrication. Also, environmentally friendly lubricants are important to balance between performance and the environmental impact of lubricants, entailing the employment of eco-friendly lubricants.
Lubricants employed to address the challenges in the mining sector
As mining operations are becoming very demanding, so is the pressure on lubricant companies to formulate
effective lubrication solutions not only to meet the required performance level (as per OEM requirements) but
also to endeavour to reduce the maintenance and operating costs while meeting health, safety, and environmental
concerns.
Let us critically examine the lubricants scenario in mining industries.
Mineral Oil-based Lubricants— Still today, a major percentage of oils used are mineral-based, owing to
high-volume usage, like hydraulic oils, engine oils, and gear oils, in various heavy-duty mining equipment and
machinery like excavators, dumpers, backhoe loaders, draglines, drilling rigs, etc. As the mining industry is
also price-sensitive, upgrading to speciality lubricants will take time, but the trend has already started due
to many tribological issues and mining professionals foreseeing and recognising the need to upgrade to
speciality lubricants, which includes synthetic lubricants.
Greases: Greases are commonly used in various mining equipment like dumpers, excavators, crushers,
draglines, etc. As these application areas are subjected to heavy loads, thereby necessitating the greases with
high Timken Loads, weld loads, including impact loading, and normal greases will not be the right candidates.
Also, moisture and dust are other challenges in the mining industry that require high water- and
dust-resistant greases, requiring strong tackifiers and additive chemistry to protect the bearings, pins,
etc., inside the machinery.
Some of the critical areas may require high-temperature greases, which are normally bentonite- or
clay-based and have high drop points or are non-dropping in nature, giving effective protection in hot
environments.
Chemical-resistant greases are also employed in the application areas wherein the chemicals are coming in
contact with the applied areas like bearings, shafts, axles, etc.
Energy-efficient lubricants play a crucial role in improving the performance, sustainability, and
cost-efficiency of machinery in the mining industry. Energy-efficient lubricants not only enhance operational
efficiency but also reduce operational costs and minimise environmental impact, making them an essential part of
modern mining operations. As the mining industry focuses more on sustainability and operational efficiency, the
demand for high-performance, energy-efficient lubricants continues to grow. Energy-efficient lubricants reduce
friction between moving parts more effectively, especially in mining equipment such as drills, trucks, and
crushers. Lower friction means less energy is required to move the parts, leading to reduced fuel consumption
and energy savings. Today, many lubricant companies have come forward with energy-efficient lubricants that
comprise mainly synthetic and semi-synthetic lubricants incorporating state-of-the-art additive technology,
nanomaterials, and nanotechnology aiming at effective boundary and mixed lubrication regimes apart from
hydrodynamic regimes.
Synthetic Lubricants: Synthetic lubricants are becoming more common in mining areas as it is the need of
the hour to combat the challenges posed in mining. Synthetic lubricants are normally based on API Base Stocks
Group IV & Group V, viz., PolyAlpha Olefins (PAOs) and esters, as these base stocks provide better and more
effective lubrication in extremes of environmental conditions of temperature, pressure, loads, moisture, etc.,
albeit these are more expensive. Another advantage of synthetic lubricants lies in their long lifecycles; for
instance, the drain interval of synthetic lubricants compared to mineral-based conventional lubricants is
manyfold, leading to less disposal of used oils/lubricants in the environment. So, synthetic lubricants in some
way also contribute to keeping the environment clean.
Biodegradable Lubricants: Today Biodegradable lubricants are encouraged and supported by not only the
mining sector but also the government at large to reduce environmental impact. Again, it puts lots of pressure
on lubricant formulators to design the biodegradable oils and greases that can withstand such extreme challenges
and render the superior performance. Esters from API Base Stock Group V are the most eligible candidates for
such lubricants, as most of these are biodegradable in nature and offer superior performance.
Proper usage and application of the right lubricants not only reduces the maintenance and operational cost but
also aims at reducing the downtime of the machines & equipment, which directly contributes to profitability in
the mining industry.
Not only do the right lubricants contribute to the efficiency and efficacy of the system, but also the various
advanced practices being introduced and adopted by the mining industry help in reducing the maintenance and
operating costs along with enhancing the uptime of the machines and equipment, thereby increasing the
reliability of the system.
Let’s delve into some of such practices.
Best Practices for Lubrication in the Mining Sector
● Lubrication Monitoring and Condition-Based Maintenance (CBM):
○ Oil Analysis: Oil analysis adds to the reliability of the machines and equipment, as regular testing of used oils can detect contamination, degradation, and wear metals. This proactive maintenance practice ensures optimal lubricant performance and enhances the reliability factor of the system.
○ Condition Monitoring Systems: IoT-based sensors and real-time monitoring systems are helping greatly in mining areas by providing valuable data on lubrication conditions, which eventually help in predicting the potential failures of the system before they occur. This not only reduces the breakdowns but adds to the reliability of the system in mining areas.
● Automated Lubrication Systems:
○ Centralised Lubrication: Many of the mining equipment and machines are equipped with centralised
lubrication systems, which ensure optimal lubrication at regular intervals without requiring manual
intervention.
○ Automatic Greasing Systems: Used in critical mining equipment like crushers and conveyors to reduce
downtime and improve efficiency.
● Lubricant Storage and Handling: Apart from lubrication, proper storage and handling of lubricants at
various mining collieries are of vital importance, as improper management can lead to contamination, which
compromises performance. It is essential to follow manufacturer guidelines for storage and handling.
● Training Personnel: Many lubricant companies conduct technical seminars and workshops on various
aspects of lubrication for front-line managers, supervisors, and operators, which ensures that workers
understand the importance of lubrication and how to apply it correctly, and such training should be on-going
programs that can make a significant difference in equipment longevity.
The Impact of Digitalisation and IoT in Lubrication
In recent years, the industrial sector has witnessed a dramatic shift driven by digitalisation and the Internet
of Things (IoT). These technologies have revolutionised many aspects of operations, including maintenance, asset
management, and process optimization. One area that has seen significant improvements due to these advancements
is lubrication. In industries like mining, where equipment operates under extreme conditions, the role of
lubrication is crucial for maintaining machinery performance and longevity. However, traditional lubrication
practices often face challenges like inefficiency, human error, and lack of real-time data.
Lubrication strategies are being reshaped due to these powerful tools as digital technologies are transforming
lubrication practices, the benefits they bring to industries like mining, and how they pave the way for more
efficient, cost-effective, and sustainable operations. By leveraging connected sensors, real-time monitoring,
predictive analytics, and automated lubrication systems, companies can optimise lubrication management, reduce
downtime, and enhance operational efficiency.
Let’s briefly discuss a few of these practices.
Predictive Maintenance with IoT:
● Today IoT devices and sensors embedded in mining equipment are being used to monitor lubrication levels and conditions, predicting maintenance needs before failures occur.
Data-Driven Decision Making:
● Today, data analytics is transforming lubrication management in mining. Mining companies can use data to optimise lubricant usage, enhance operational efficiency, and reduce costs.
Integration with Machine Learning and AI:
● Machine learning algorithms are also improving lubrication strategies by analysing vast amounts of data to predict when lubrication should be replenished or replaced.
But the mining sector is still to adopt and implement these techniques and practices fully, as the spread of mining areas and, therefore, the equipment and machinery are far off, and it will take its time to upgrade to these practices.
Conclusion
In the mining industry, where operational efficiency and machinery reliability are paramount, lubrication
solutions play a critical role in ensuring equipment longevity and minimising costly downtime, which entails a
continuous need for research & innovation in the field of lubrication to meet the increasing demands of the
mining industry while addressing operational and environmental challenges. From reducing friction and wear to
preventing system failures, effective lubrication directly impacts productivity, safety, and maintenance costs.
There is also the need for the mining industry to encourage digitalisation and cutting-edge technological
lubricants, including energy-efficient lubricants, which can not only help in the reduction of maintenance,
operational, and downtime costs but also enhance the system's reliability and efficiencies.
The challenges faced by the mining industry—such as extreme operating conditions, harsh environments, and the
push for sustainability—necessitate lubrication strategies that are not only efficient but also highly
adaptable. In this context, modern lubrication technologies, such as automated systems, IoT-enabled sensors, and
predictive analytics, offer significant advantages. These innovations enable real-time monitoring, precise
application, and data-driven decision-making, which ultimately enhance the overall effectiveness of lubrication
practices.
Looking ahead, the future of lubrication in the mining industry lies in continued advancements in
digitalisation, predictive maintenance, and sustainability. As companies embrace these technologies, they will
be better equipped to meet the evolving demands of the industry, driving both operational excellence and
environmental responsibility. In the end, investing in the right lubrication solutions is not just a matter of
equipment maintenance; it’s an investment in the continued success and resilience of the mining industry itself.
References
https://www.elsevier.com/open-access/userlicense/1.0/
https://www.sciencedirect.com/science/article/pii/S0301679X17302359
https://www.futuremarketinsights.com/reports/mining-lubricants
https://en.wikipedia.org/wiki/Bharat_Coking_Coal
About the Author-
Vivek Gupta
Vivek Gupta is a Mechanical Engineer with an MBA, bringing over 25 years of extensive industry experience in the
lubrication field including managing lubricant solutions to Mining Industry. His expertise spans Specialty and
Super-specialty lubricants, Automotive & Industrial lubricants, Base Stocks ( API Group I, II, III, IV, V),
Synthetic Esters and Lubricant additives. Currently, serving as the National Key Accounts Manager at Coraplus
India (Vestcorp Holdings Group Company). Over the years, he has held key roles in reputed companies such as
AVI-OIL, Valvoline Cummins, etc. wherein he developed deep insights into the lubrication industry and its
evolving needs. You can contact Mr Vivek Gupta at vivek.g@coraplus.com/vivek414@rediffmail.com
Mr Vivek Gupta
National Key Accounts Manager | Coraplus India