Sustainability and Carbon Footprints in the Steel Industry
Overview of India's Steel Industry: -
India ranks as the second largest producer of steel globally, with a total output of 140 million tons in 2023. It also stands as the second largest consumer, with steel consumption reaching 133 million tons in the same year, according to data from World Steel.
Growth of Steel Consumption and Economic Impact: -
The consumption of steel in India has grown substantially, rising from 6.5 million tons in 1968 to 133 million tons by 2023. This increase mirrors the expansion of India’s economy, where GDP has surged from $0.25 trillion to $3 trillion over the same period. The steel sector contributes approximately 2% directly to India’s GDP, with its indirect impact being even more significant due to the heavy reliance of various industries on steel.
Diversity in Steel Production: -
India’s steel industry is marked by diversity, with a mix of different-sized facilities in both primary and secondary steelmaking sectors. Various technologies are employed in the production process, including the Blast Furnace(BF-BOF), Electric Induction Furnace (EIF), and Electric Arc Furnace (EAF). This variety provides a broad perspective on the sector’s role in India’s economic growth and the range of production methods used.
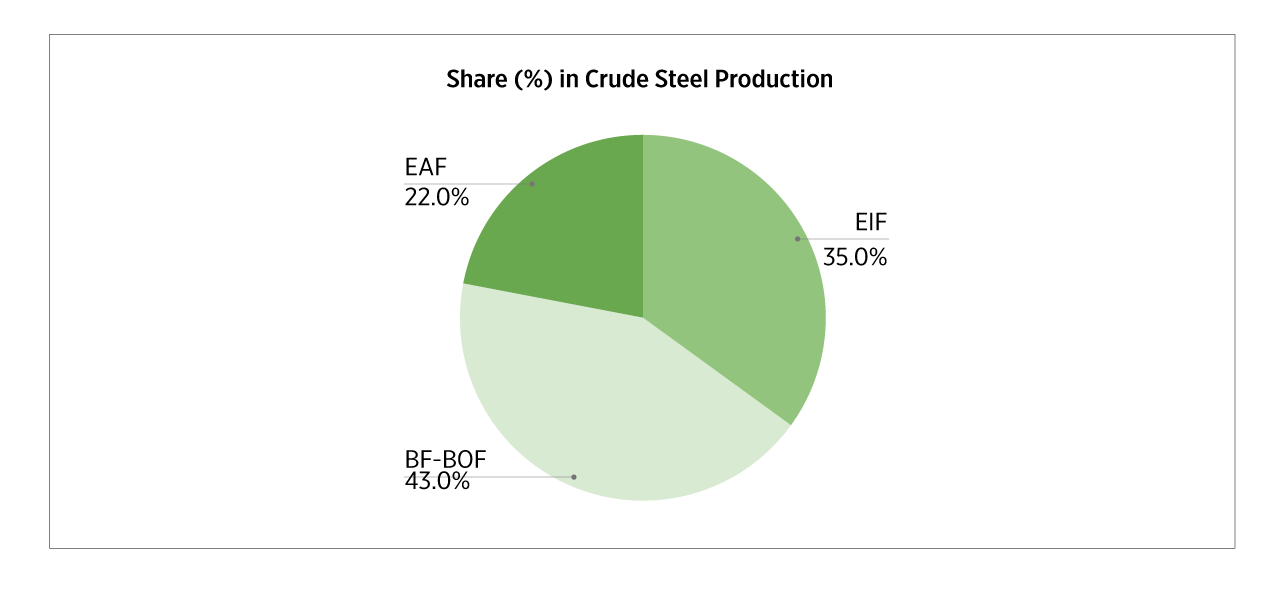
Fig 1: Graph showing: Route-wise Steel Production. Source - JPC
Addressing Global Climate Change
Global governments are increasingly focusing on tackling the pressing issue of climate change. Every year, organizations studying climate change stress the need for stronger efforts to cut greenhouse gas (GHG) emissions. Consequently, many countries have set ambitious goals to significantly reduce emissions, aiming for net zero. India, for instance, has committed to achieving net zero emissions by 2070.
Major Contributors to Greenhouse Gas Emissions
Several key sectors are responsible for global GHG emissions, including energy, agriculture, waste management, industry, forestry, and land use. Of these, the energy sector is the largest contributor, accounting for 73.2% of emissions (36.2 gigatons). Within the energy sector, Industry accounts for 24.2% (12 GT), buildings 17.5% (8.7 GT), and transport 16.2% (8 GT).
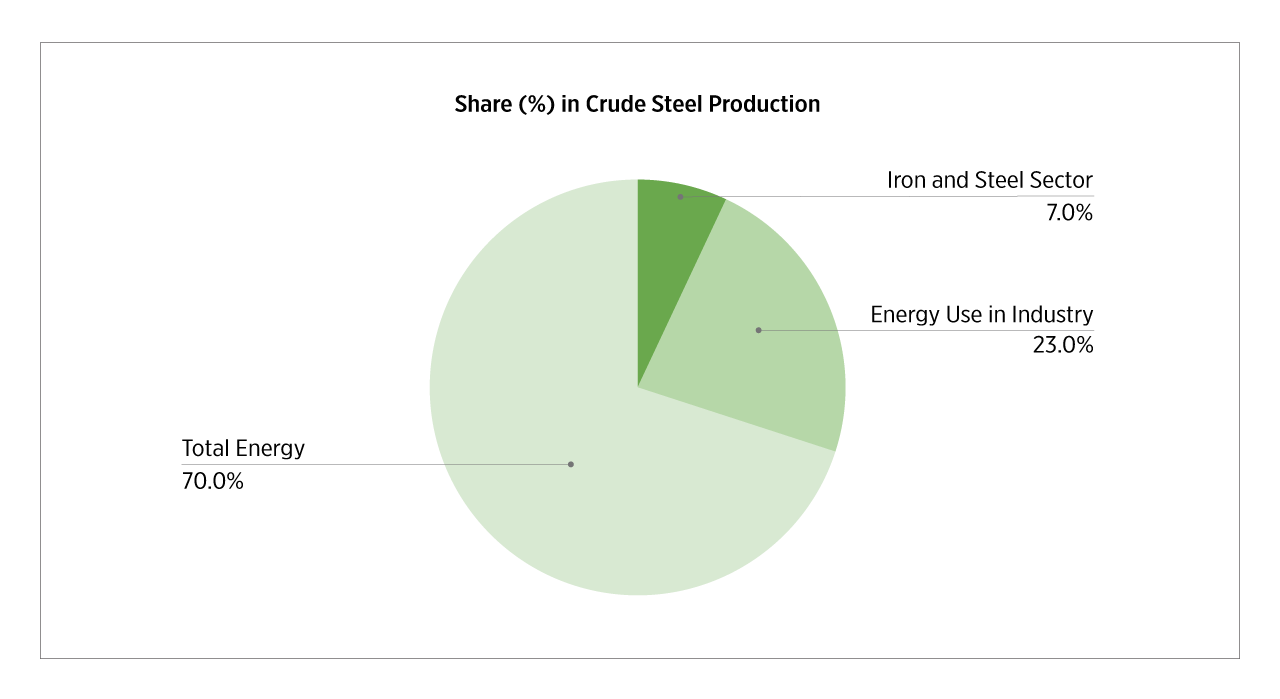
Fig.2: Source IEA
The Role of the Iron and Steel Sector
The iron and steel sector is a significant contributor to global emissions, responsible for 7.2% (3.5 GT) of the total global emission in 2016. This underscores the need to focus on this sector in efforts to reduce GHG emissions and combat climate change.
Understanding Carbon Intensity in Steel Production
The carbon intensity of steel production is influenced by the method used to convert iron ore into finished steel and the type of fuel employed in the manufacturing process.
Comparing Steel Production Technologies
The BF-BOF technology, which uses coking coal not only as a fuel but also as a reducing agent, is more polluting compared to the DRI technology. The DRI process uses EAF’s to produce steel, making the DRI-EAF route less harmful to the environment. Globally, the BF-BOF method is seen as more challenging to decarbonize than the DRI-EAF route.
The Indian Context: DRI and Emissions
In India, the situation is different. Most DRI units, accounting for 82% of the country's DRI production, are small and medium-scale operations that use coal-based rotary kilns to produce iron. In India, DRI is used not only as a raw material in EAFs but also frequently in induction furnaces, which produced 30% of the steel in the country in 2020.
Emission Targets and Current Status
In India, the current emission factor for the BF-BOF route is already close to the 2030 emissions target outlined in the National Steel Policy, 2017. This suggests that the BF-BOF technology is on track to meet national goals for reducing emissions, despite its higher pollution levels compared to other methods.
Future Emissions in India's Steel Sector
The future emissions profile of India's steel sector by 2030 will be shaped by factors such as sectoral targets, fuel transitions, and technological advancements. We have estimated emissions under four different scenarios by varying these factors.
-
Steel Scrap Recycling Policy and its Impact
The 2019 Steel Scrap Recycling Policy anticipates that 35-40% of the steel production capacity (300 million tonnes per year) and production (255 million tonnes per year) envisioned for 2030 will rely on the EAF and IF methods. This assumption is applied across all scenarios. Currently, 55% of India's crude steel is produced using the EAF/IF method, which is highly polluting due to the use of coal-based rotary kilns. -
Scenario 1: Business-as-Usual (BAU)
The BAU scenario considers the projected production growth and technology share for 2030 but uses current emission factors. This scenario assumes no significant changes in technology or fuel use. -
Scenario 2: National Steel Policy Targets
The second scenario assumes that the steel industry meets the emission reduction targets set by the National Steel Policy of 2017. This scenario represents a low-carbon growth pathway for 2030, considering the same projected production growth and technology share for 2030 as outlined in the policy. Within the 35% share of DRI-EAF/IF production, it is assumed that gas-based steel production will increase to 15%. -
Scenario 3: Voluntary Carbon Intensity Targets
The third scenario builds on the second by assuming that large steel companies achieve their voluntary carbon intensity targets, further enhancing the low-carbon growth pathway. This scenario also assumes an increase in gas-based DRI-EAF steel production to 15%.
These scenarios provide a framework for understanding how different approaches and targets could shape the future emissions profile of India’s steel sector by 2030.
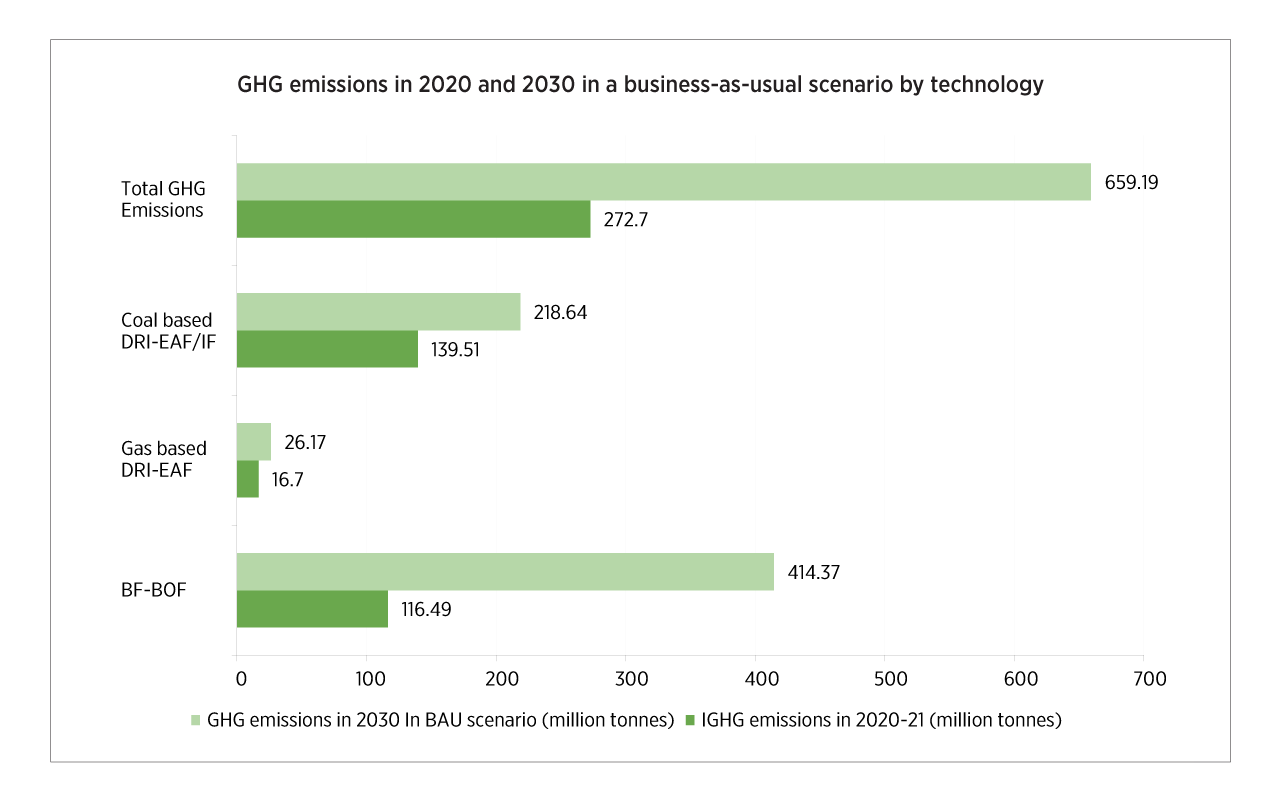
Fig. 3: Source IEA
Pathways for Reducing Carbon Intensity in the Steel Sector
The iron and steel industry needs a well-defined plan to reduce emissions, even beyond current low-carbon goals. To explore the possibilities, we have outlined various technology options for reducing emissions in this sector.
Sector-Wide Improvements
Certain strategies can be applied across all steel production methods to reduce emissions. This section discusses some of these approaches.
Technologies for Reducing Emissions and Resource Use
There are several technologies that can help lower carbon emissions from steel plants. The Ministry of Steel has identified a list of such technologies, including:
- Coke Dry Quenching (CDQ):Generates power from waste heat during the CDQ process.
- Sinter Plant Heat Recovery: Captures waste heat from the sinter cooler for power generation.
- Bell-less Top Equipment (BLT): Enhances efficiency in blast furnaces.
- Top Pressure Recovery Turbine (TRT): Generates power from high-pressure gases in blast furnaces.
- Pulverized Coal Injection (PCI) System:Improves blast furnace efficiency by injecting pulverized coal.
- Hot Stove Waste Heat Recovery: Recovers heat from blast furnace stoves.
- Dry Type Gas Cleaning Plant (GCP): Cleans gases from blast furnaces more efficiently.
- De-dusting Systems: Reduces dust in cast houses or stock-houses.
- Converter Gas Recovery in BOF:Captures and reuses gases from basic oxygen furnaces.
- Energy Monitoring Systems: Tracks and manages energy use for better efficiency.
- Secondary Fume Extraction in Steel Shops:Reduces emissions during steel melting.
- Regenerative Burners in Reheating Furnaces: Saves energy in rolling mills.
- Hot Charging Process: Directly charges hot products into rolling mills, reducing reheating needs.
- Direct Rolling Process: Eliminates the need for reheating furnaces, saving energy.
- Energy-Efficient Technology for Hot Strip Mills: Utilizes flexible thin slab casting and rolling.
- Near Net Shape Casting: Reduces waste and energy use in casting processes.
- Variable Voltage Variable Frequency (VVVF) Drives: Enhances efficiency in electric motors.
The Ministry of Steel has reported that implementing these technologies led to a reduction in CO₂ emissions between 2014 and 2016.
Future Technologies for the Steel Industry:
- Green Hydrogen Technology: India is shifting from coal to green hydrogen in Direct Reduced Iron (DRI) Processes. This transition is part of the Green Hydrogen Mission, which aims to decarbonize the economy, reduce fossil fuel imports, and establish India as a leader in green hydrogen. The initiative includes a budget of Rs. 455 Crore up to 2029-30 for pilot projects in low-carbon steel.
- Carbon Capture, Utilization, and Storage (CCUS): This technology captures CO₂ from steelmaking for repurposing or storage. In India, CCUS can enhance oil recovery, create useful chemicals, or store CO₂ underground, though it faces challenges like high costs and the need for robust infrastructure.
- Iron Ore Beneficiation: This process improves the quality of domestic iron ore, which typically has lower iron content. By using AI-driven optimization and advanced techniques, energy efficiency in steel production can be enhanced, reducing dependence on imported high-grade ore and lowering emissions.
- Biomass Utilization: Replacing coal or coke with biomass or biochar as a carbon-neutral alternative in steelmaking can significantly reduce the sector's carbon footprint.
- Electrification of Steelmaking Processes: Using renewable energy for processes like heating, rolling, and finishing can decrease fossil fuel use and CO₂ emissions. India is increasingly investing in renewable energy, with efforts to integrate solar and wind power into steel production.
- Digitalization and Industry 4.0: The adoption of AI, IoT, and data analytics in steel manufacturing can improve efficiency and reduce emissions, and many companies are already investing in these technologies.
Conclusion
In conclusion, the steel industry in India, as one of the world’s largest producers and consumers, plays a pivotal role in both economic growth and environmental sustainability. The industry's significant contribution to greenhouse gas emissions underscores the urgent need for targeted strategies to reduce carbon intensity. While traditional steelmaking technologies, such as the Blast Furnace-Basic Oxygen Furnace (BF-BOF), present considerable challenges in decarbonization, newer methods like Direct Reduced Iron (DRI) using Electric Arc Furnaces (EAF) offer promising pathways to lower emissions.
India's commitment to achieving net-zero emissions by 2070 and the proactive steps outlined in the National Steel Policy highlight the sector's readiness to embrace change. The integration of advanced technologies, such as Green Hydrogen, Carbon Capture, Utilization, and Storage (CCUS), and the electrification of steelmaking processes, will be crucial in this transition. Additionally, the emphasis on digitalization and Industry 4.0 will further enhance efficiency and reduce the carbon footprint of steel production.
As the industry moves forward, continued innovation, investment in sustainable technologies, and adherence to stringent emission targets will be key to achieving a balance between economic growth and environmental stewardship. The pathways explored in this document provide a comprehensive framework for the future of India's steel industry, ensuring its contribution to global efforts in combating climate change while sustaining its critical role in the nation’s development
About the Author
Annup Kashyap has over a decade of experience in the steel industry
and is currently the Assistant Director (Technical) at the Indian
Steel Association. He has published more than 60 reports on steel
development and has played a significant role in key projects focused
on raw materials, Global and Domestic Economic outlook, environmental
management, and sustainability. He holds a B. Tech in Mechanical and
Automation and a Postgraduate Diploma in Environmental Law and Policy.
Contact Mr. Anup Kashyap at anup.kashyap24@gmail.com
Mr. Annup Kashyap
Assistant Director(Technical) | Indian Steel Association