Mission Impossible - Maximizing bearing life at minimized lubricant volumes
In wood pellet and animal feed production, the details of pelletizing processes have long been a challenge, hindered by technological stagnation. However, by digging into the underlying principles of friction, lubrication, and Total Cost of Ownership (TCO), a new era of efficiency is dawning.
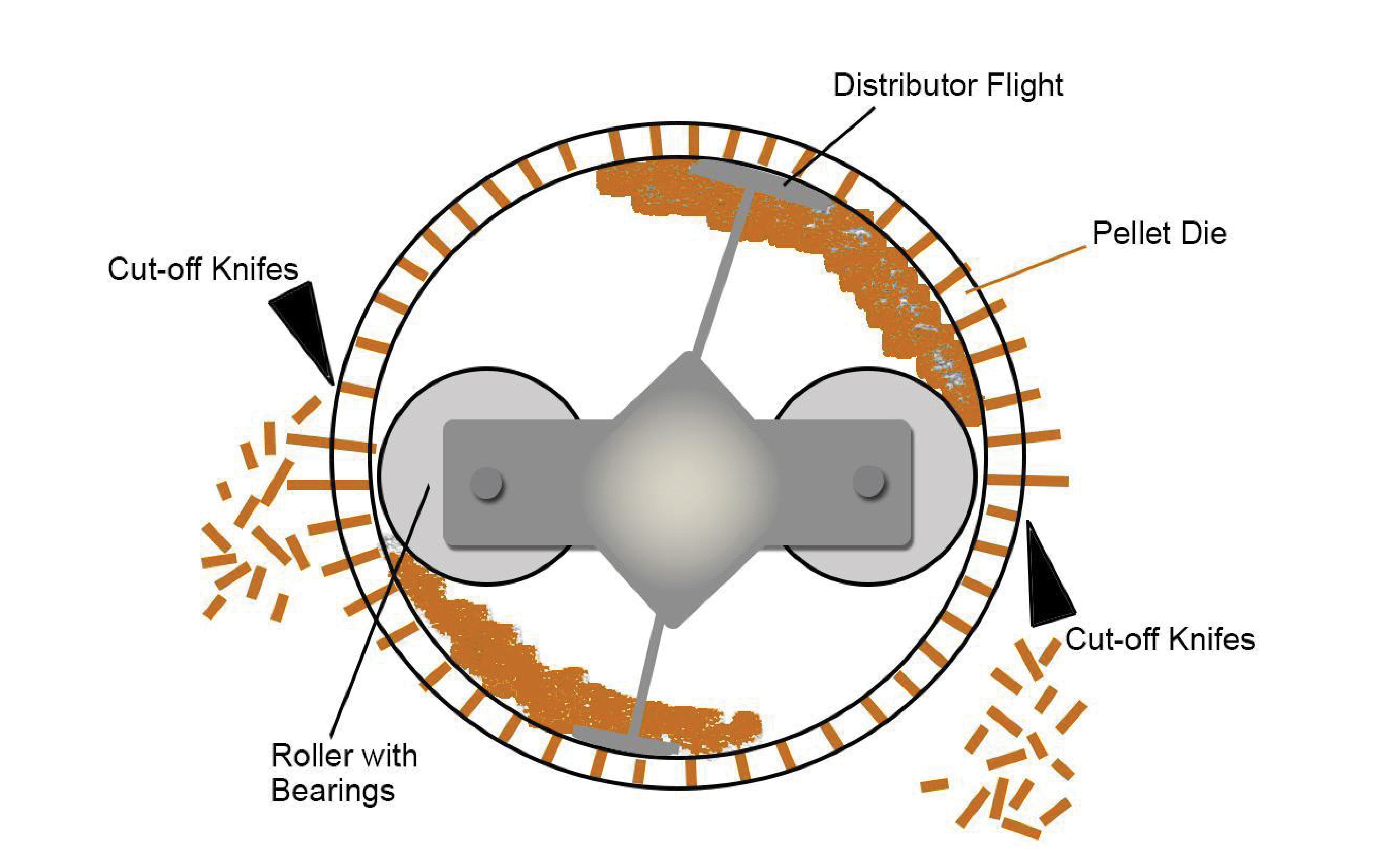
Fig. 1 pellet production principle
Understanding the Root Causes
Traditionally, the challenges stem from the demanding conditions endured by roller bearings within wood and animal feed pellet mills. These conditions, ranging from extreme pressures to corrosive atmospheres, create a hostile environment for optimal bearing performance. While the load on animal feed pellet mills are very low, minerals increase the wear on shells, fine dust can cause bearing contamination, and steam can cause corrosion. In wood pellet production load, vibrations and overall wear on equipment are severe. Conditions amplify when instead of white fiber, bark is included in the raw material. The interaction between the roller bearings and the surrounding environment, compounded by the repetitive stresses of the pelletizing process (Fig. 1), leads to accelerated wear and tear. Historically, solutions have involved excessive greasing and oversized, inadequate lubrication systems. Unfortunately, these approaches contribute to elevated TCO, including higher maintenance costs, unplanned stoppages, and logistical hurdles.
Total Cost of Ownership (TCO) is a comprehensive financial estimate that encompasses all direct and indirect costs associated with acquiring, operating, and maintaining a particular asset or system over its entire lifecycle. This includes not only the initial purchase price but also expenses such as installation, training, maintenance, repairs, downtime, and disposal or decommissioning costs. By considering all relevant costs beyond just the upfront investment, TCO provides a more accurate and holistic assessment of the true economic impact of owning and utilizing an asset. This enables businesses to make more informed decisions regarding investment, procurement, and operational strategies, ultimately optimizing resource allocation and maximizing return on investment.
Breaking the Deadlock
To unlock efficiency, two solutions emerge: Tribology and advanced lubrication systems. Tribology, the interdisciplinary field encompassing the study of friction, wear, and lubrication, offers profound insights into overcoming the mechanical and chemical limitations faced in pelletizing processes. By leveraging the principles of tribology, researchers and engineers have developed innovative lubrication solutions tailored to the specific demands of pellet mills.
One promising avenue lies in the integration of high-performance greases containing solid lubricant particles, such as ceramic-based lubricants. These advanced lubricants exhibit superior lubricating properties and offer enhanced protection against wear and corrosion (Fig. 2). By forming a durable coating on the bearing surfaces, ceramic-based greases mitigate frictional losses and reduce the risk of premature failure. Moreover, their exceptional thermal stability and resistance to oxidation make them well-suited for the high-temperature operating conditions encountered in pellet mills.
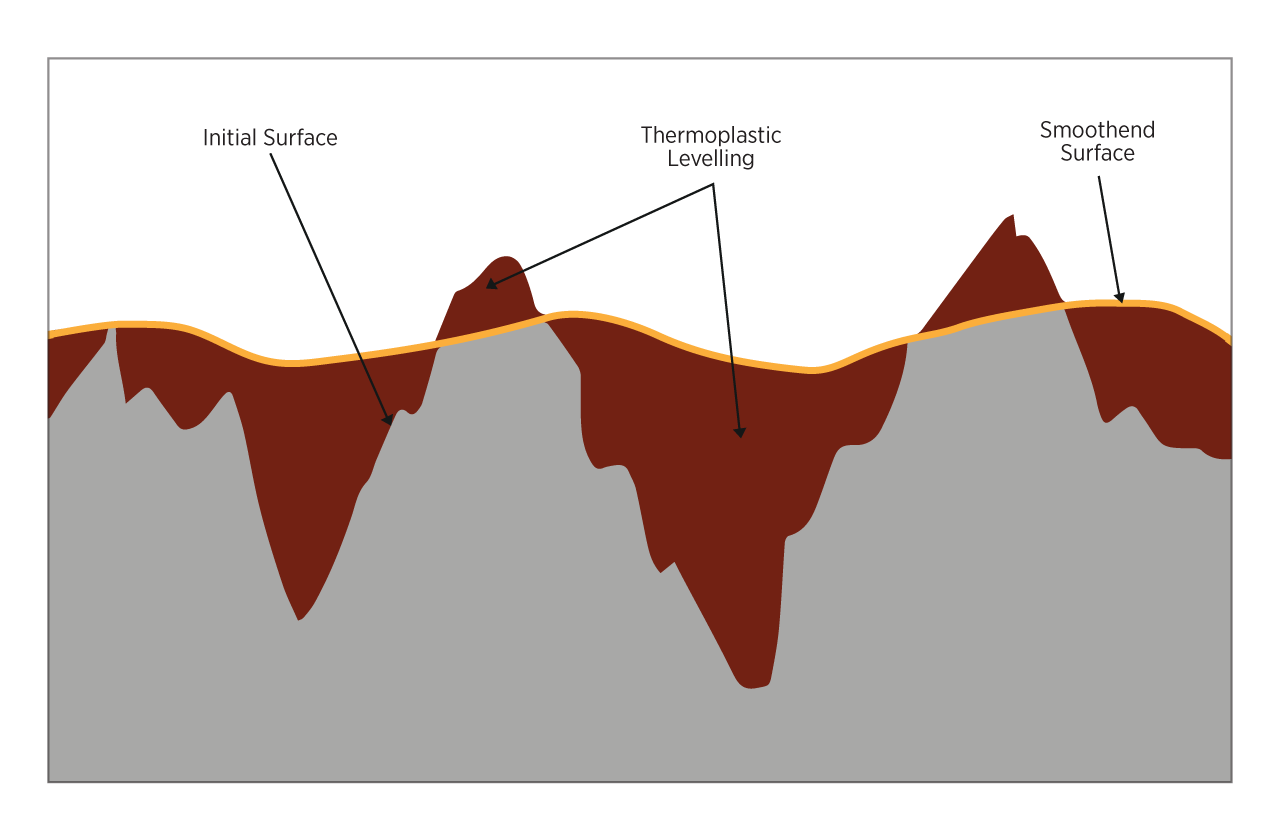
Fig. 2 Surface coating with ceramic particles.
Meanwhile, advanced automated lubrication systems represent another critical facet of the solution. These sophisticated systems are designed to ensure precise and consistent lubricant application, thereby minimizing the risk of over-greasing or under-lubrication. By employing programmable controllers and precision dispensing mechanisms, these systems can tailor lubricant delivery to the specific requirements of each bearing and component within the pellet mill (Fig. 3). Additionally, integrated monitoring and diagnostics capabilities enable proactive maintenance and troubleshooting, further enhancing equipment reliability and uptime.
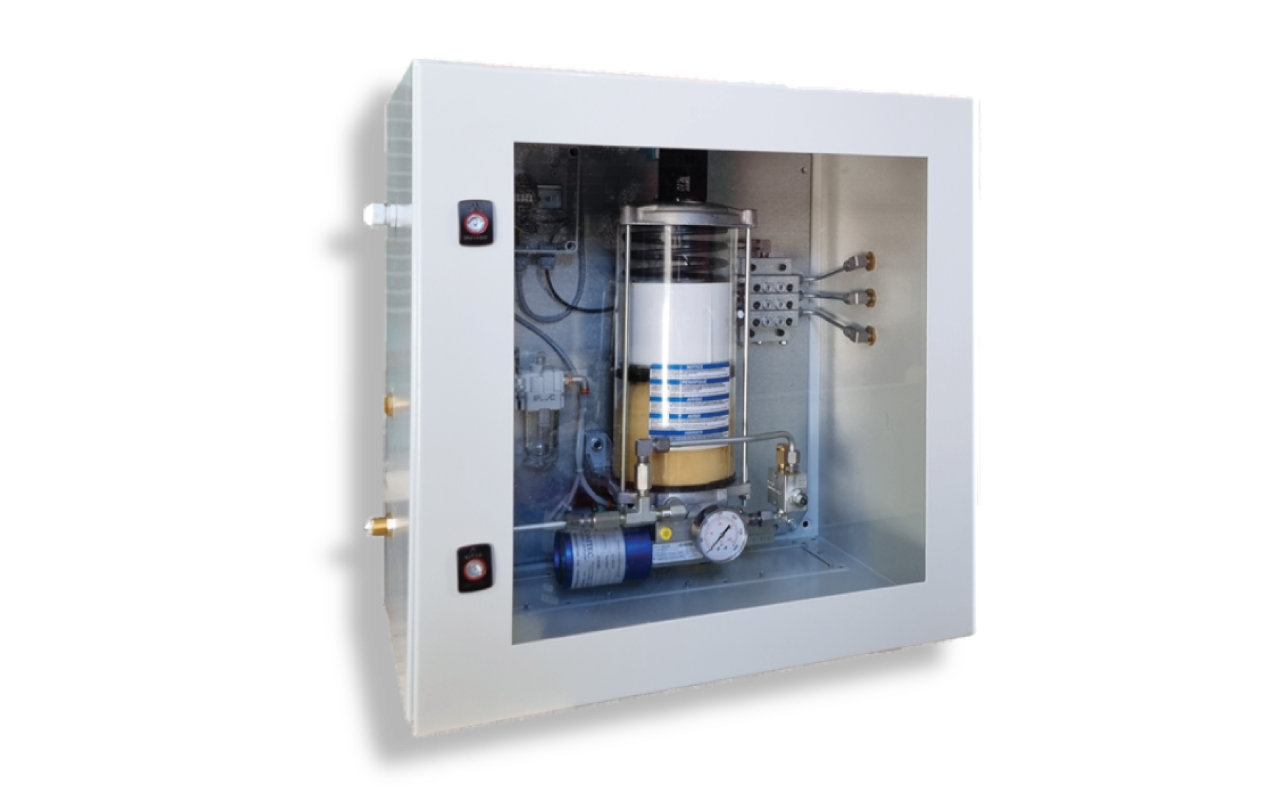
Fig. 3 Re-designed automated lubrication system
Achieving Efficiency Gains
Implementing these solutions yields tangible benefits across multiple dimensions. High-performance greases have demonstrated remarkable reductions in grease consumption, with some formulations boasting up to a 96.58% decrease over extended production periods. This substantial reduction in lubricant usage translates directly into cost savings for pellet producers, while also reducing waste and environmental impact.
Moreover, the optimized lubrication regime enabled by advanced automated lubrication systems leads to significant improvements in equipment reliability and longevity. By ensuring proper lubrication of critical components, such as roller bearings and drive mechanisms, these systems mitigate the risk of premature failure and unplanned downtime. The result is a more robust and resilient pelletizing process, capable of meeting the demands of continuous operation with minimal disruptions.
Furthermore, the adoption of advanced lubrication solutions contributes to broader sustainability goals by reducing resource consumption and minimizing environmental footprint. By optimizing lubricant usage and extending equipment lifespan, pellet producers can reduce their overall energy consumption and carbon emissions, contributing to a more sustainable and environmentally responsible industry (Fig. 4).
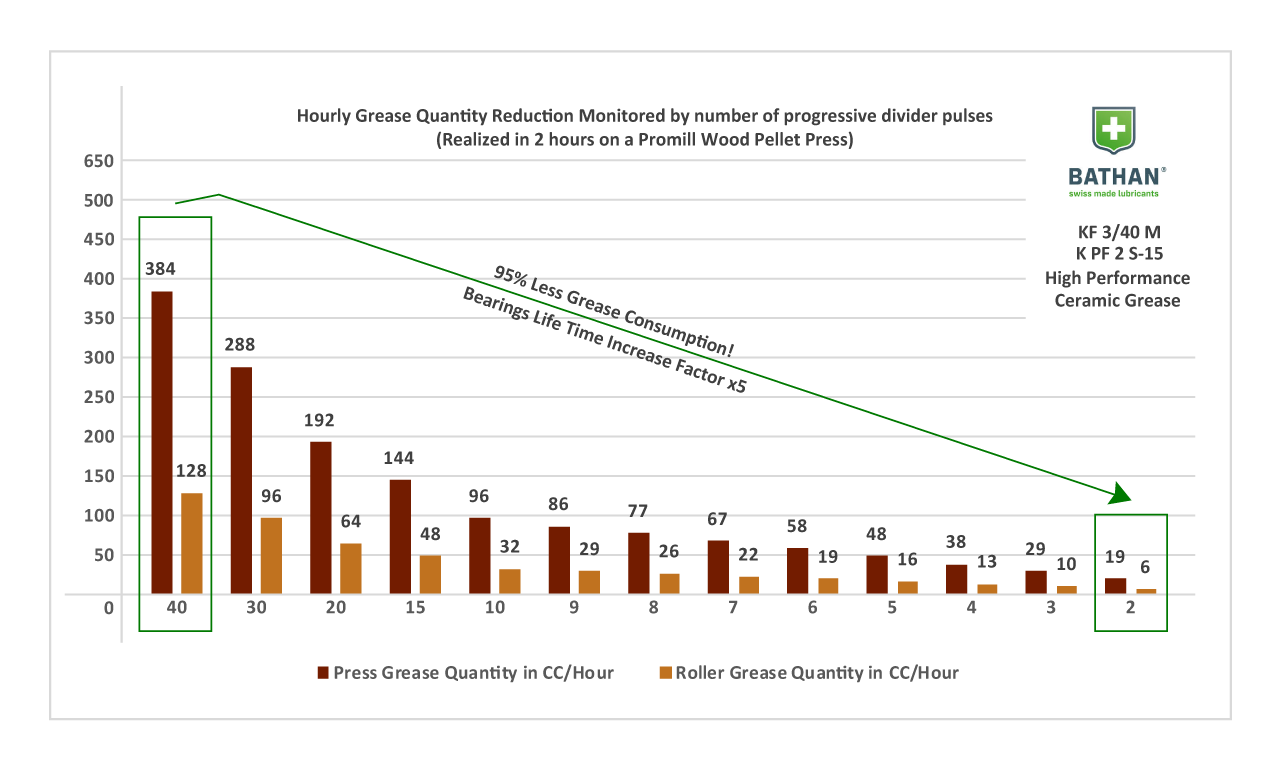
Fig. 4 Reduction in grease consumption and increase in bearing life
Re-thinking Storage
A 95% reduction in grease consumption has significant implications for storage practices within a facility. Here's how:
-
Space Optimization:
With drastically reduced grease volumes, the need for storage space is significantly diminished. This allows facilities to optimize their storage areas, potentially freeing up valuable floor space for other purposes such as additional equipment or operational activities. -
Inventory Management:
Lower grease consumption simplifies inventory management processes. Facilities will need to procure and store smaller quantities of grease, reducing the complexity of inventory tracking and management. This can lead to more efficient stock control and reduced risk of overstocking or obsolete inventory. -
Storage Costs:
Reduced grease consumption directly translates to lower storage costs. Facilities can save on expenses related to storage infrastructure, such as shelving, containers, and dedicated storage areas. Additionally, lower grease volumes mean reduced requirements for environmental controls (e.g., temperature and humidity regulation) within storage facilities. -
Handling and Transportation:
Smaller quantities of grease are easier to handle and transport within the facility. This reduces the labor and equipment required for grease-handling activities such as loading, unloading, and transportation between storage and application points. Furthermore, it may lower the need for specialized handling equipment or safety precautions associated with large grease volumes. -
Environmental Impact:
Decreased grease consumption aligns with sustainability goals by reducing the environmental impact of grease storage. Smaller quantities of grease mean lower risks of spills or leaks, minimizing the potential for environmental contamination and simplifying cleanup efforts in case of accidents.
Overall, a 95% reduction in grease consumption has far-reaching implications for storage practices, offering benefits such as space optimization, streamlined inventory management, cost savings, improved handling efficiency, and reduced environmental impact.
Embracing a New Era
By embracing advancements in tribology and adopting precise lubrication systems, the pellet industry can break free from technological stagnation and unlock new levels of efficiency and productivity. This transformative shift not only delivers immediate cost savings and operational improvements but also positions pellet producers for long-term success in an increasingly competitive market. With a focus on innovation and sustainability, stakeholders can pave the way for a future characterized by enhanced performance, reduced costs, and environmental stewardship.
About the Author
Alain Skrobala is a seasoned professional in the realm of lubricants
and lubrication systems, with a career spanning over three decades.
Currently serving as the Head of Sales at Bathan AG, he brings
extensive expertise and leadership to the table. Roles with Bijur
Delimon International and Carl BECHEM honed his skills in sales,
marketing, and strategic planning. Throughout his career, he has
demonstrated a profound understanding of market dynamics, coupled with
a strategic approach to product management. Having navigated through
various positions of increasing responsibility, he has developed a
reputation for fostering strong client relationships and driving
business growth. His dedication to excellence and passion for
innovation continue to be the driving forces behind his success in the
lubricant industry.
Contact Mr. Alain Skrobala at a.skrobala@bathan.ch